It turns out that a dairy barn can become a family getaway without much ado, design-wise. Consider this rural Virginia property, where the livestock habitats were flipped into living spaces without adding or removing major walls. The cattle pens on the first floor of the two-story bank barn became the living/dining/cooking areas, and the second-story feed lot was reimagined as two bedrooms. Adjoining the barn at a right angle, the manure shed and silage chute is now a screened porch, while an attached tractor shed became a guest room. And the milking parlor across the courtyard was repurposed as a playroom and entertaining zone.
As Mark McInturff, FAIA, and Peter Noonan, AIA, tell it, the new spaces nested easily into the old—programmatically, at least. The builder, Sam Morgan of Added Dimensions, has a different perspective. He describes the pitch-perfect “farm to table” renovation as “the simplicity on the other side of complexity.” Says Sam, “There was nothing simple about this; we were there close to 18 months. However, the shape of the building didn’t change much. What I found interesting was that although they were changing the use completely and modifying this old dairy barn, the owners never wanted to go too far that it would lose that resemblance.”
That is why Mark says, “In a funny sense, it designed itself. All the materials we used, particularly on the exterior, had already been used on the complex. It’s not an aggressive contrast at all.”
The owners, an active family, asked for a basic second-home program: gathering room, bedrooms, screened porch. But while the fit was straightforward, the renovation, of course, required gutting the 1980s-era post-and-beam timber building and surgically inserting steel to bring it up to code. It also involved demolishing the hefty troughs and chutes that were integral to the concrete slab. “The perimeter of the building was left essentially intact, but parts of the slabs were 2 feet thick and had to be removed in some places,” Sam says.
Open-Minded
Bank barns are built into a slope, creating a walk-out upper floor. The cows came in on the lower level, while feed was stored on the second floor and dropped down through a chute. With only a ladder to connect the two stories internally, the architects made a center cut in the upper floor and inserted a semi-custom circular stair that bisects the two bedrooms. Downstairs, it lands at a double-height dining room and entry flanked by the open kitchen and living room. “Because we took out a third of the second floor for the stair, we needed a new steel structure to keep everything standing,” Peter says.
That metal spiral became a focal point, its sculptural qualities accentuated by natural light. Glass doors on the upper landing open to a patio outside the bedrooms, and a large skylight cut into the lower floor’s existing shed roof reinforces the house’s cross axis. “We put the big skylight on the same centerline as the big opening in the second floor,” Peter says. “Above that is a new cupola with four windows. We took off the existing one and modified the dimensions slightly.” Positioned above the entry and dining area, the skylight brings sunlight deep into the first floor, where light also pours in through a wall of floor-to-ceiling windows that face the south courtyard. “The south-facing skylight and glass wall do a lot of work,” says Mark.
Barn-to-house renovations may present a more delicate challenge, real or perceived. Those who worry about any lingering odors associated with livestock might be relieved to find that the adjoining manure shed is now a porch with retractable screens. The architects opened the ceiling while preserving the grid of rafters, and new oak planks line the underside of the pitched roof. They also replaced two cupolas that bring light into the center of the porch to match those on the old milking parlor that faces it across the courtyard. The screened porch culminates in a guest bedroom (the former tractor shed), and behind the building, a small guest bath bump-out with a split-pitched roof balances an existing bay at the opposite end of the elevation, which holds a mudroom next to the kitchen.
Old Is New
If the 2,500-square-foot interior was “designed with an eraser,” as Mark puts it, the exterior, too, retains its original massing and materials. Roofing was replaced in-kind—black standing-seam metal on the lower roofs and cedar shingles on the main barn roof, which was resheathed for energy efficiency. “Part of modernizing the main barn was that we needed to leave the shape of the structure but infill-frame the entire wood frame portion of the second level,” Sam says. “Seventy-five percent of what’s behind the board and batten is new framing.”
On the barn’s west end-wall, window openings in the solid stone were reworked for better alignment, and closed-cell foam insulation within minimalist framing maintains a thin profile. “The stone mason tweaked things; you can’t really see where the old blends with the new,” Sam says. On the barn’s other three exterior walls, the board and batten siding was updated with new proportions. The architects also preserved the look of whitewashed stone that appears here and there, including along the barn’s east foundation and on the screened porch. “Some stone is whitewashed, some is not. We didn’t change that,” Mark says.
Interior materials—wood, stone, and plaster—were selected for their informality, warmth, and wearability. The painted board and batten siding wraps inside along the hovering upper level, while slightly rustic oak covers the floors and most walls, including the kitchen’s cabinets and storage wall. After insulating the tractor shed/guest suite’s floor and roof, the crew simply touched up the whitewashed stone walls. “The owners didn’t want to cover them up” by adding insulation, Sam says. “The idea was that the guest space would be used infrequently.”
Perhaps the most intriguing aspects of farm buildings are that they make their own statement, are oriented toward the outdoors, and often occur in clusters, suggesting a small village. Here, the negative space between the house and former milking parlor is given over to a new pool and other outdoor activities, with thermal bluestone paving to unify the whole. The milking parlor’s new playroom and entertainment space opens to the pool courtyard through an approximately 20-foot-wide folding door system.
“The pool negotiates the change in grade between the milking parlor and barn,” Peter says. “One end is flush with the pool deck; closer to the barn, two steps go down and the pool coping becomes a bench to sit on and interacts with the screened porch.” On the south border, an old fieldstone wall marks the path (now a driveway) that the cattle took to the milking parlor and out the other side.
For both the builder and the architects, this project was a welcome change from their typical work on Washington, D.C.’s tight urban lots, and for Mark’s team, a checked box. “Over the years we’ve wanted to do a barn renovation but had never done one. The conversion was demanding in terms of the detailing, but all in all, the barn laid itself out as a house very easily,” he says.
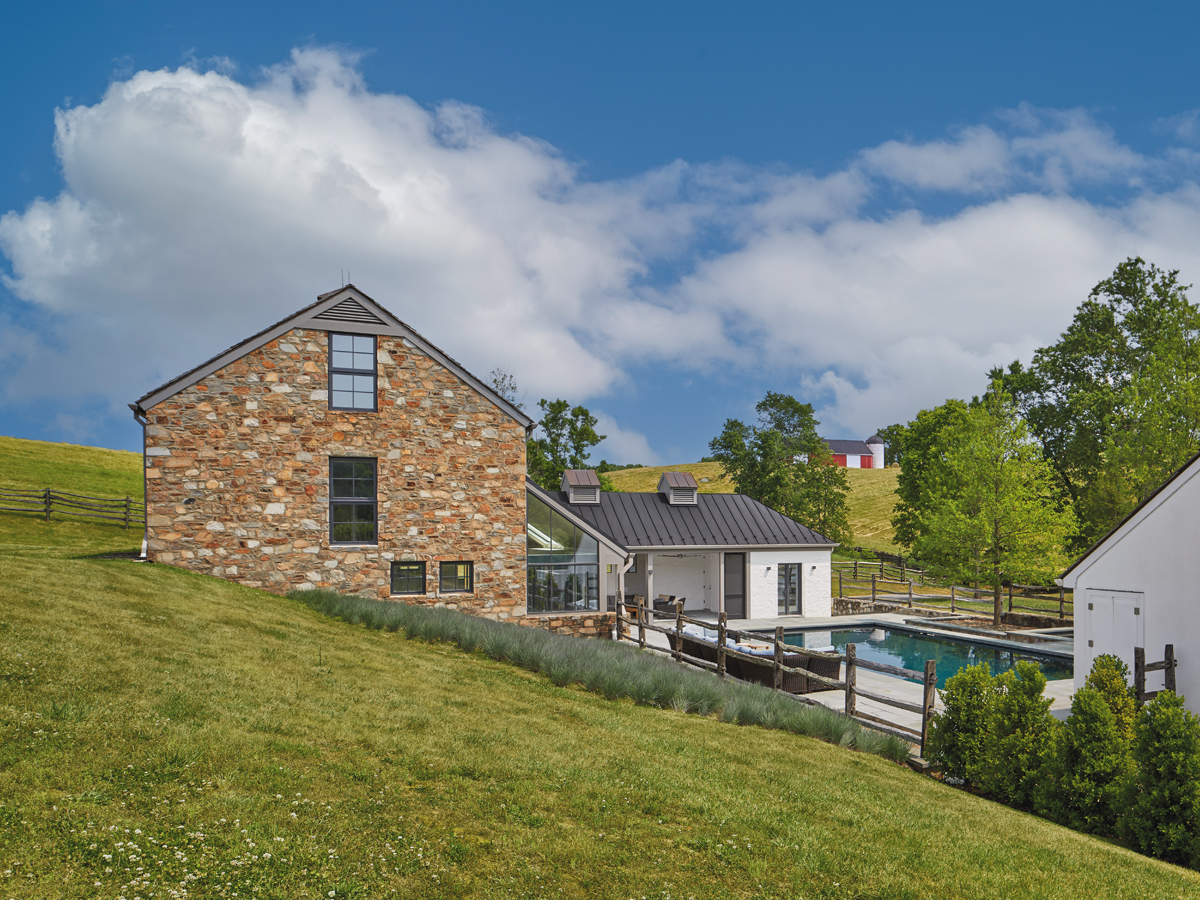
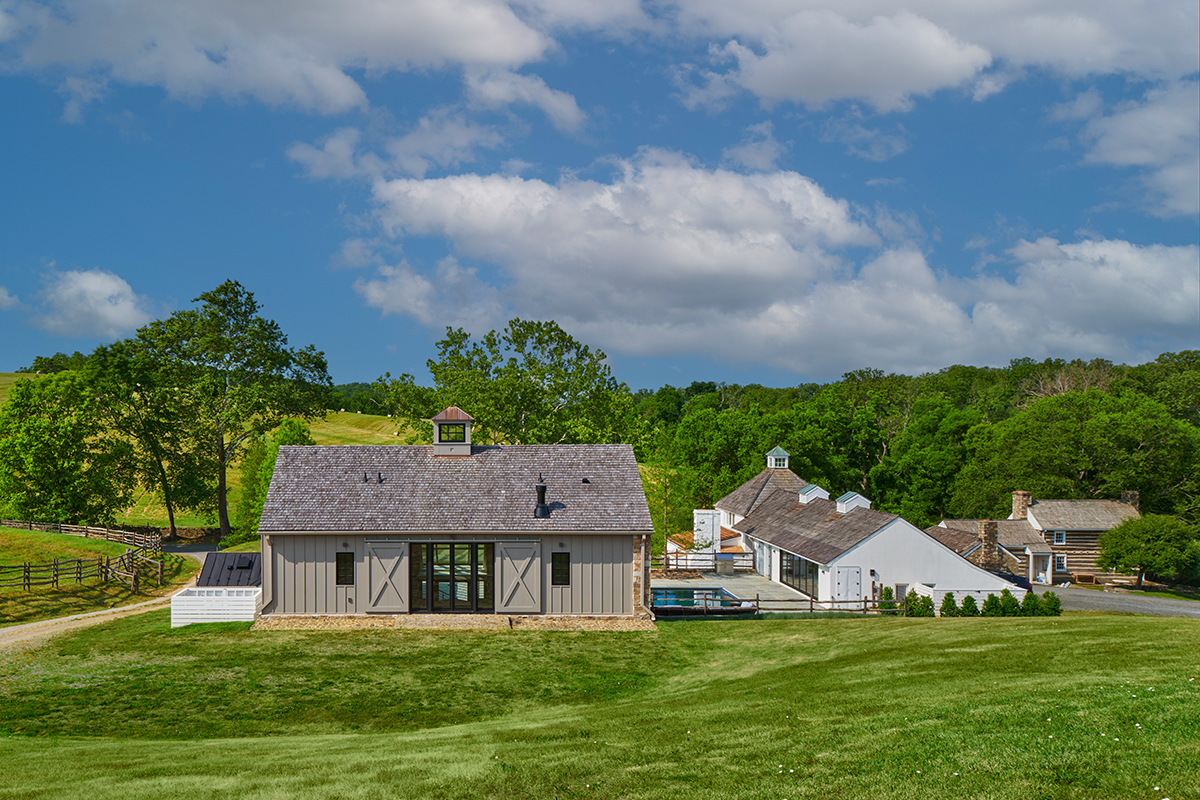
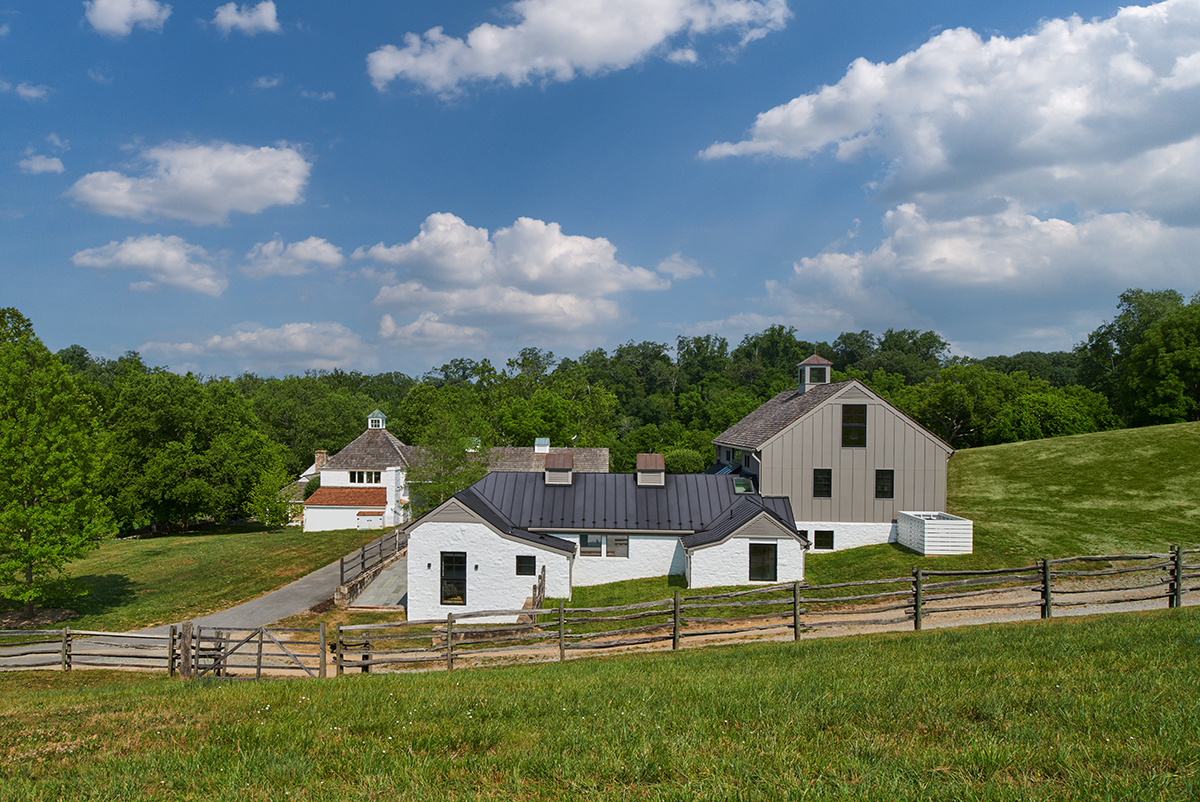
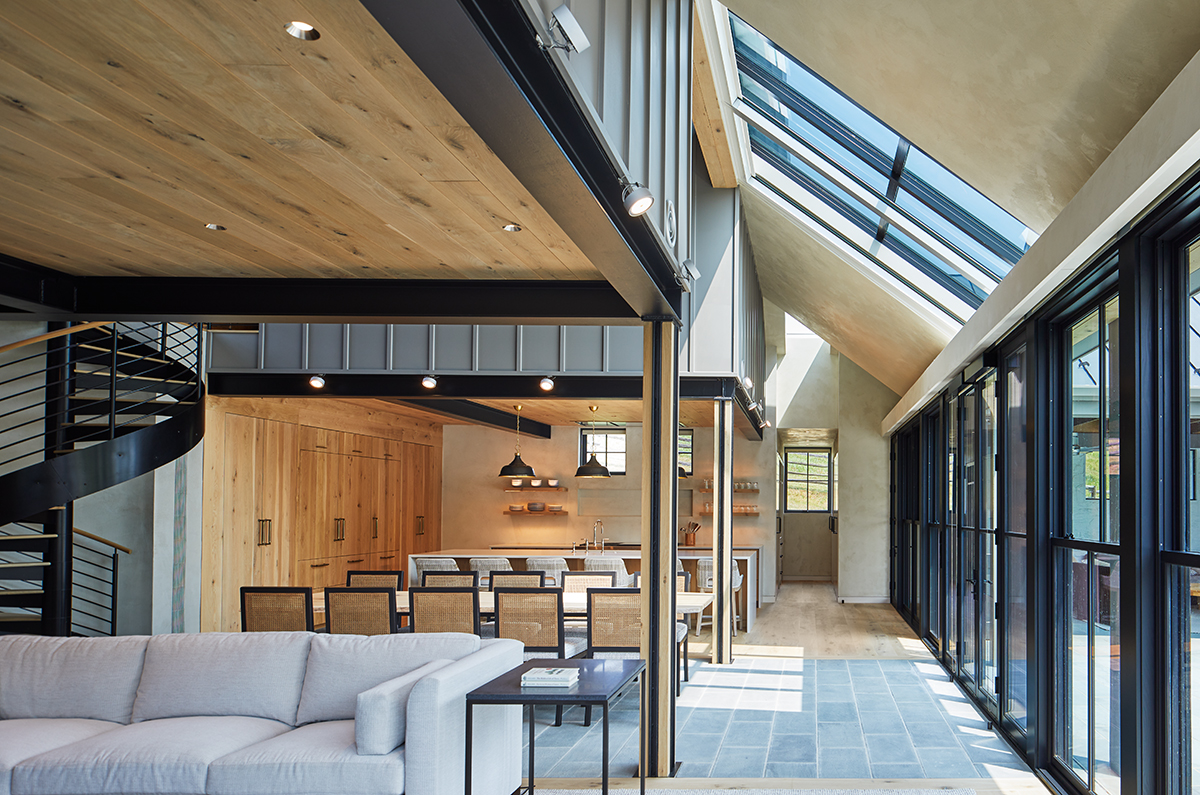
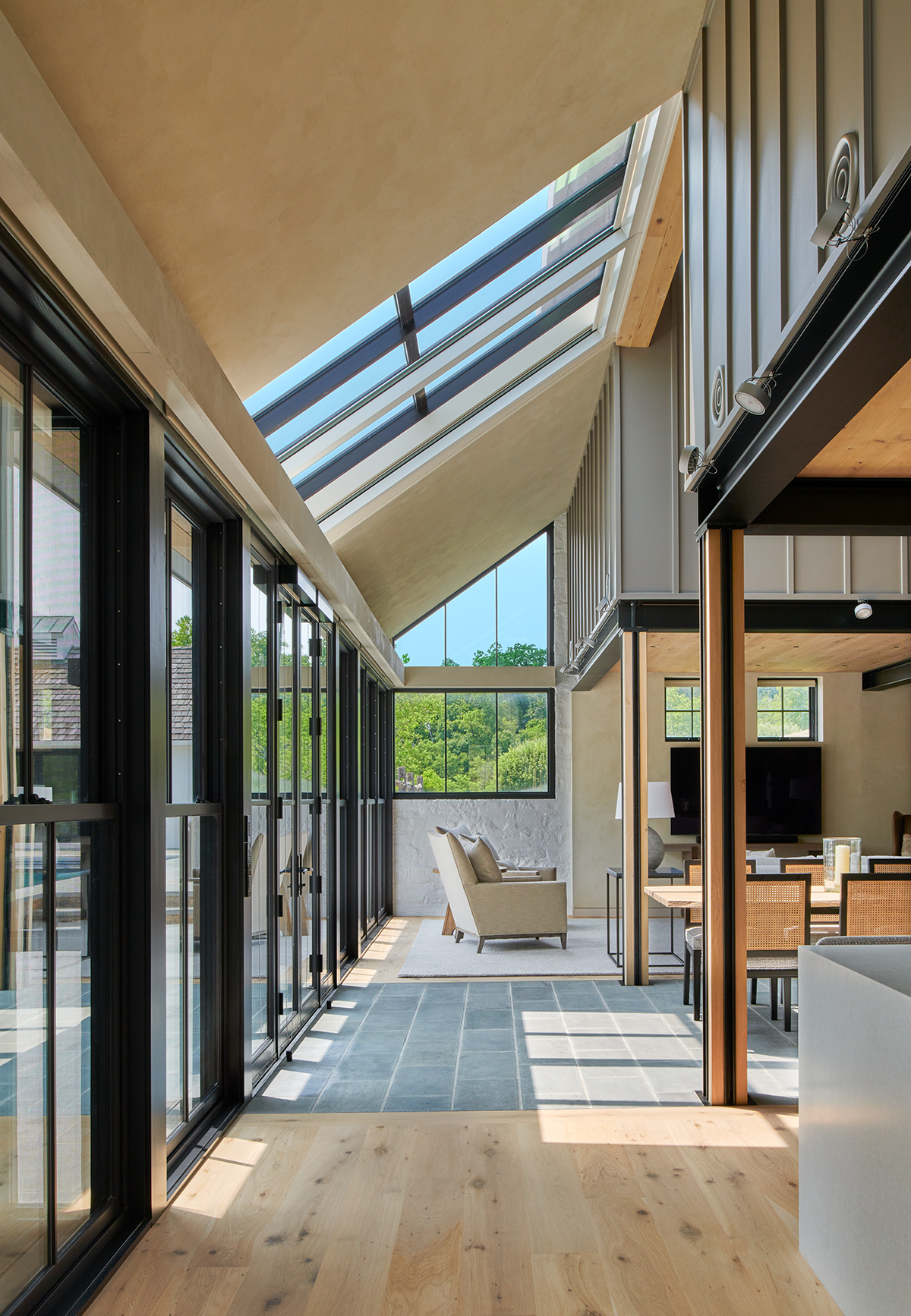
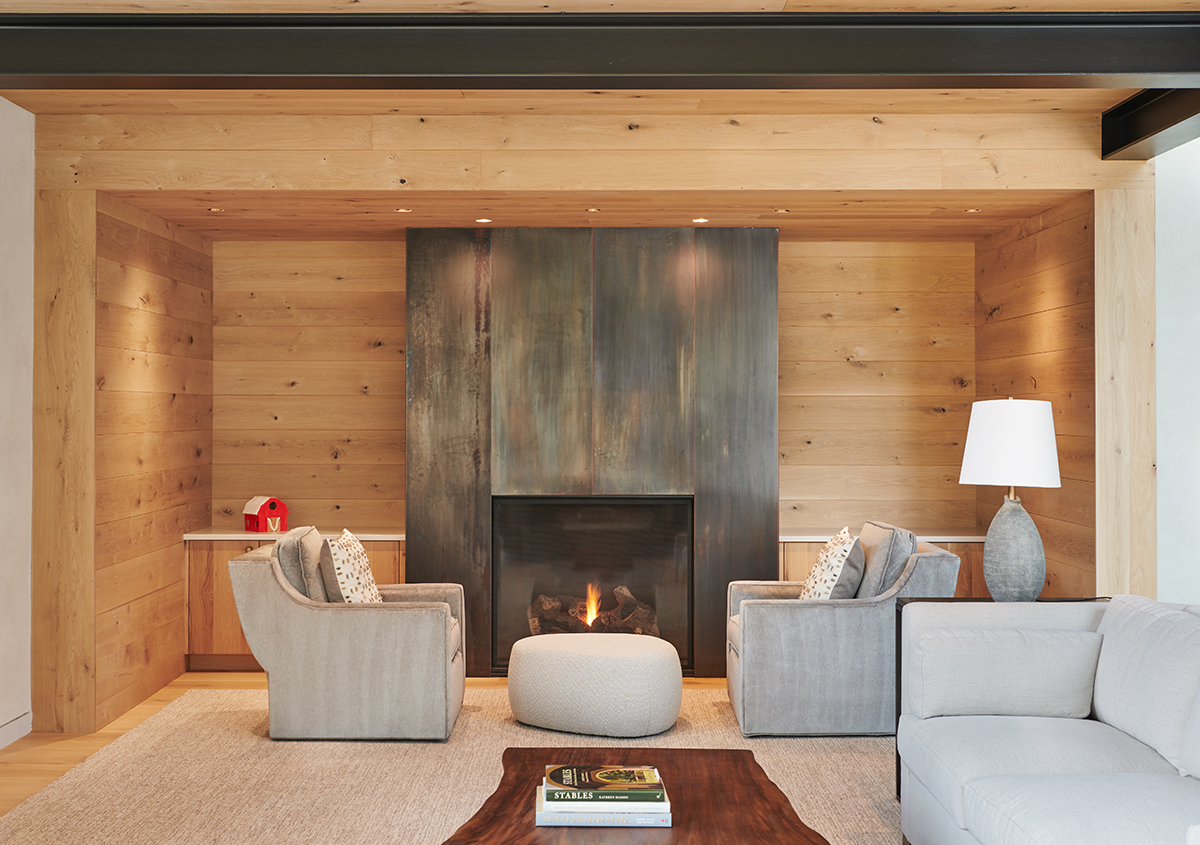
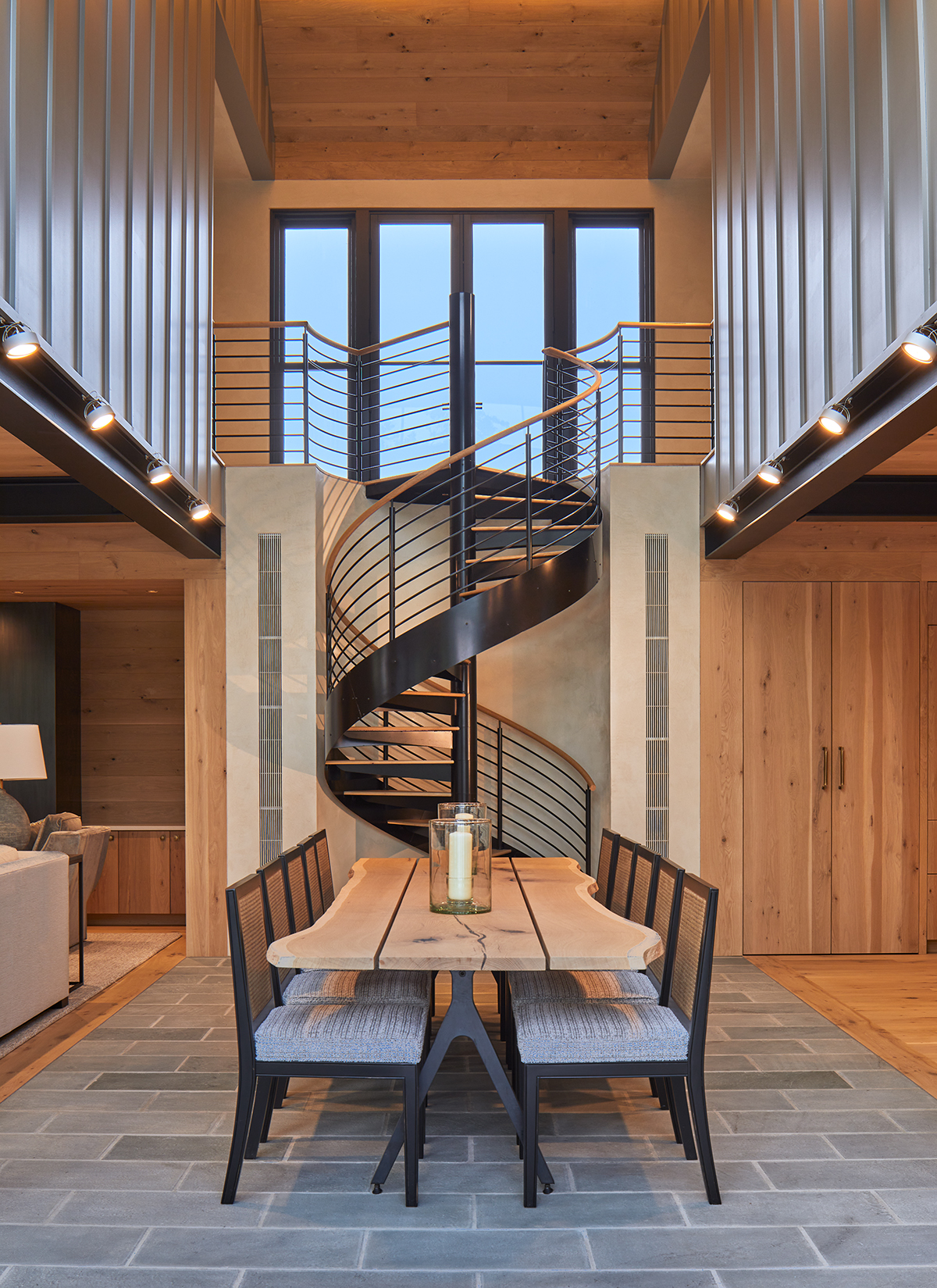
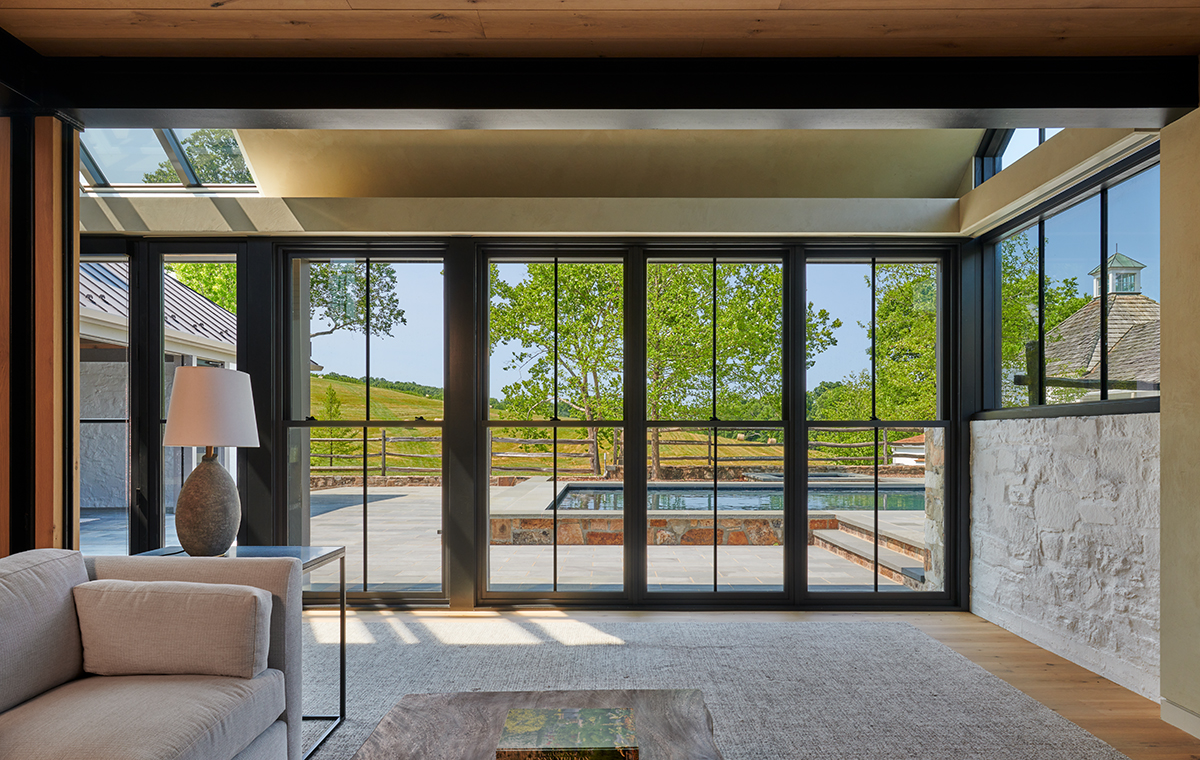
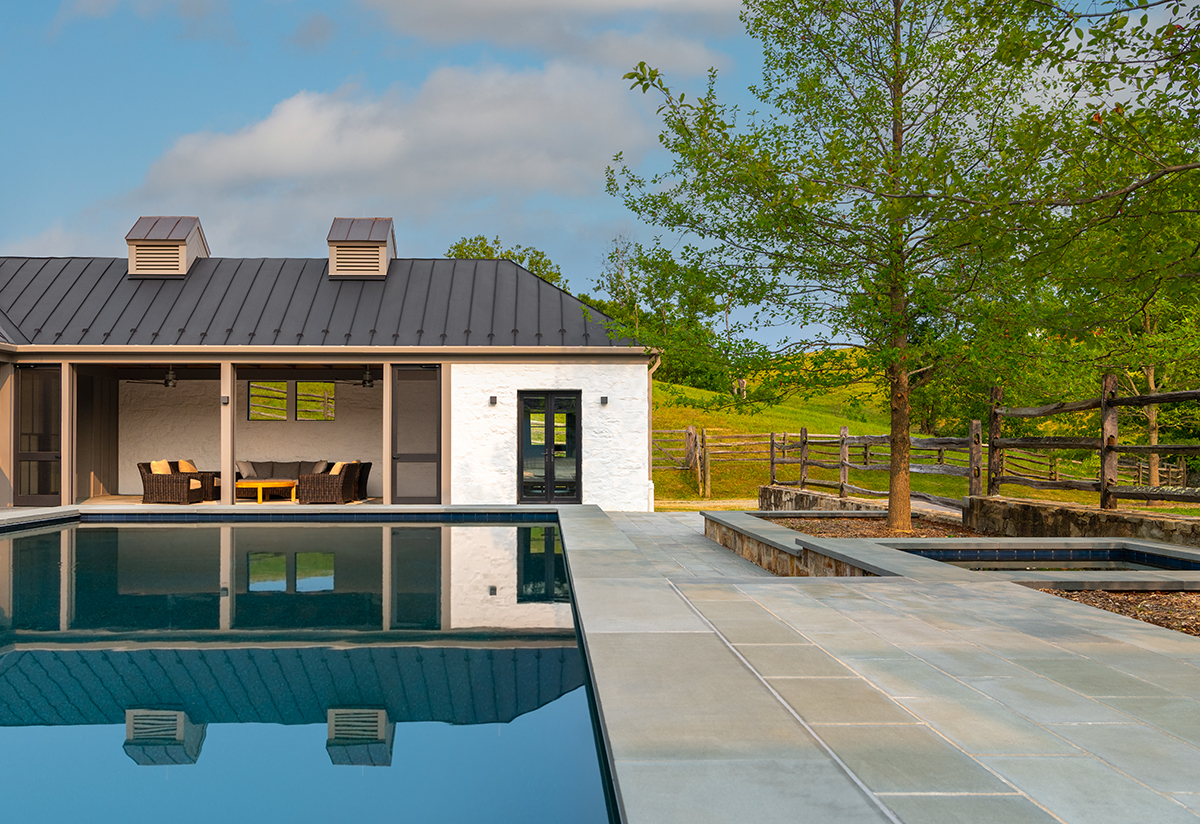
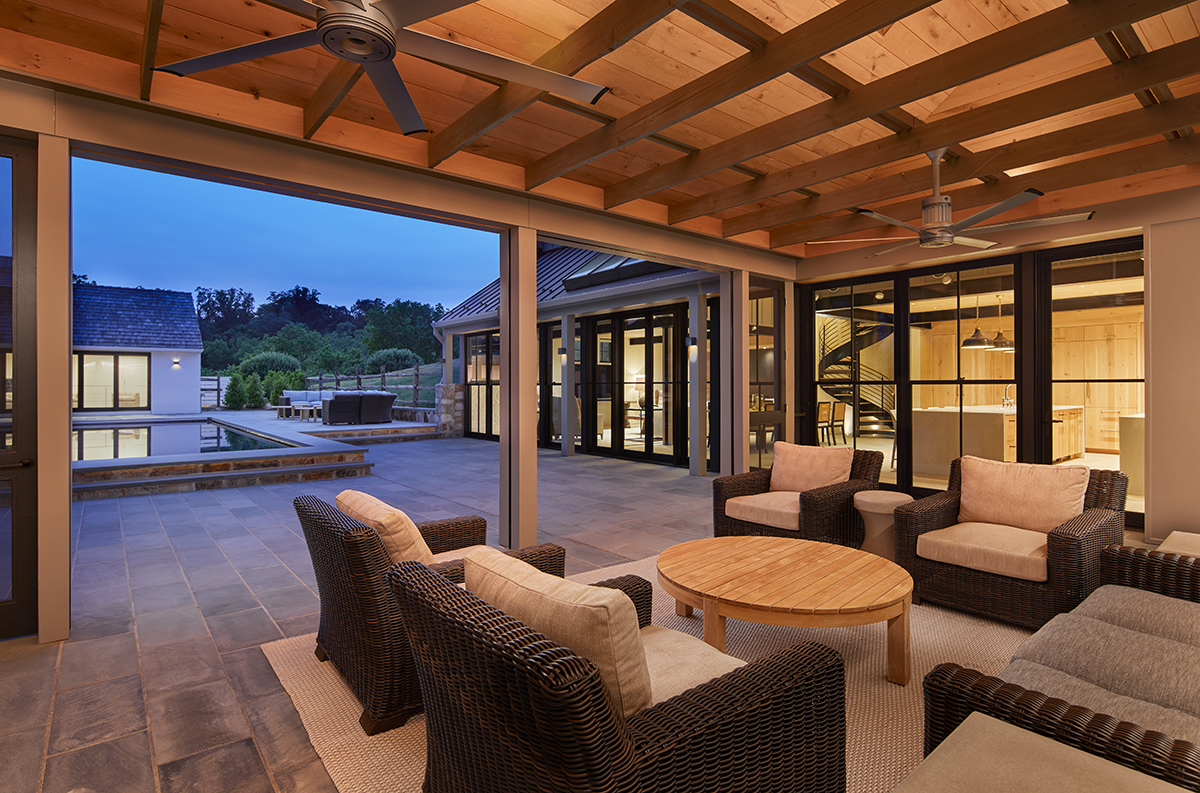
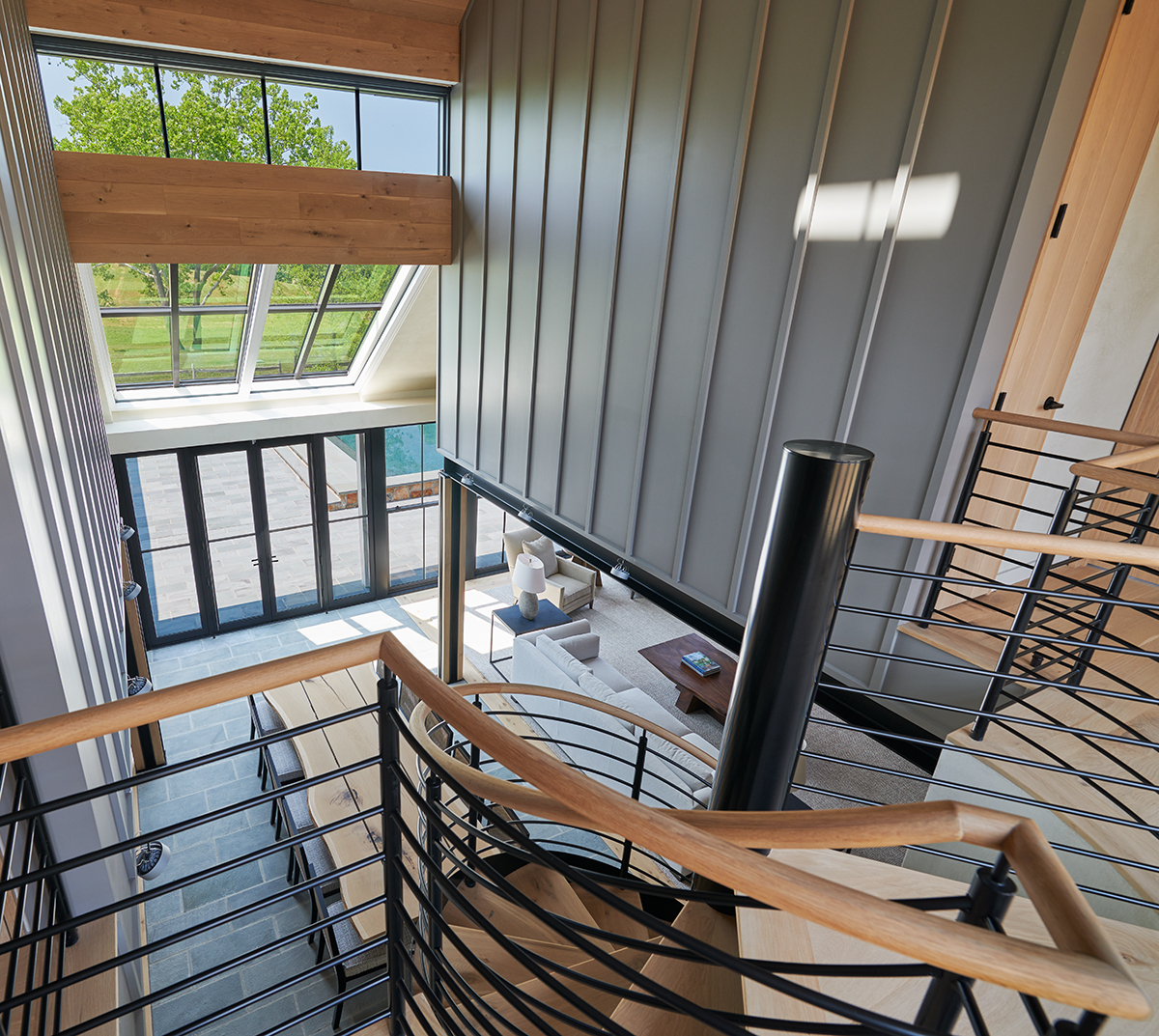
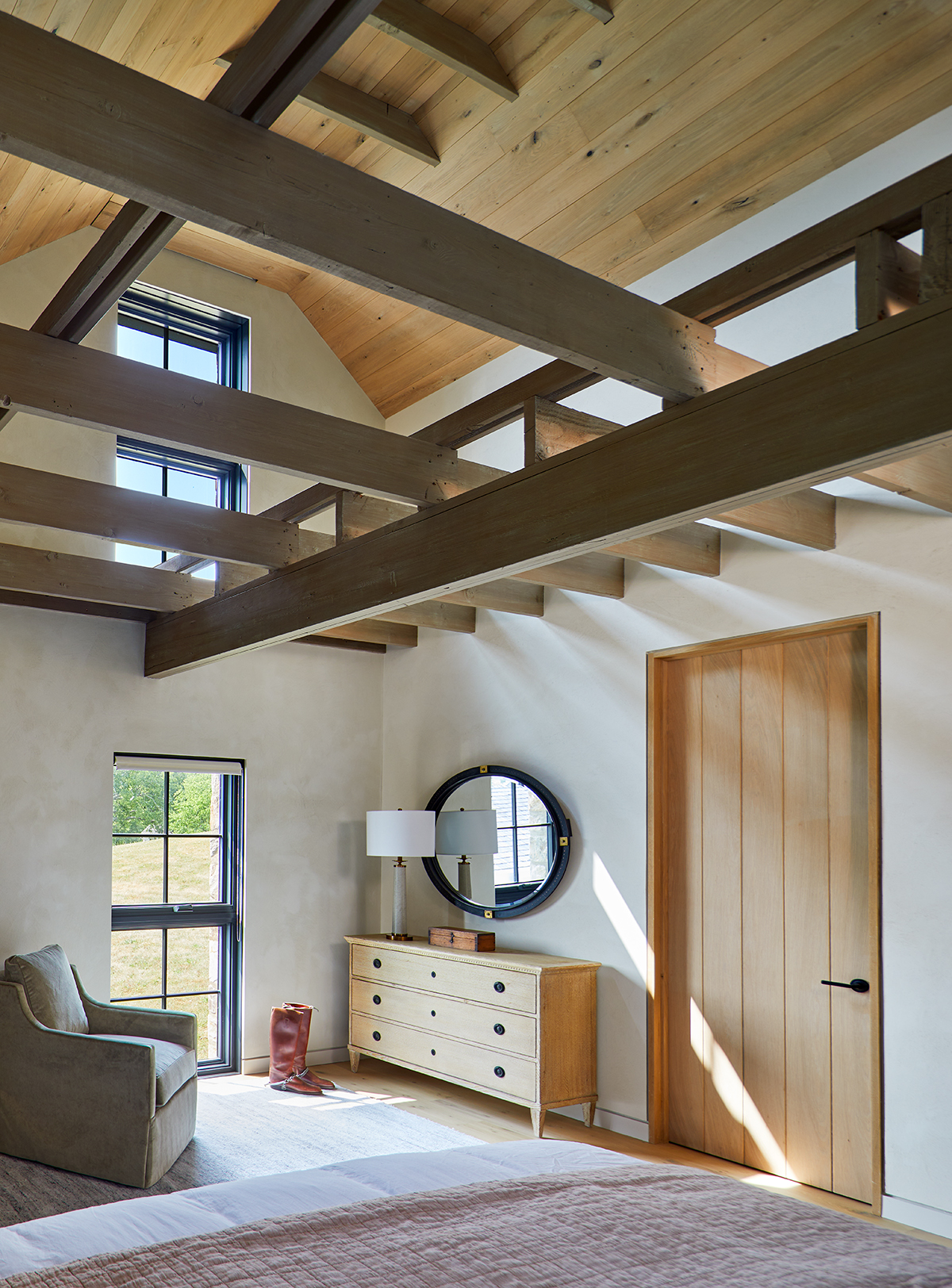
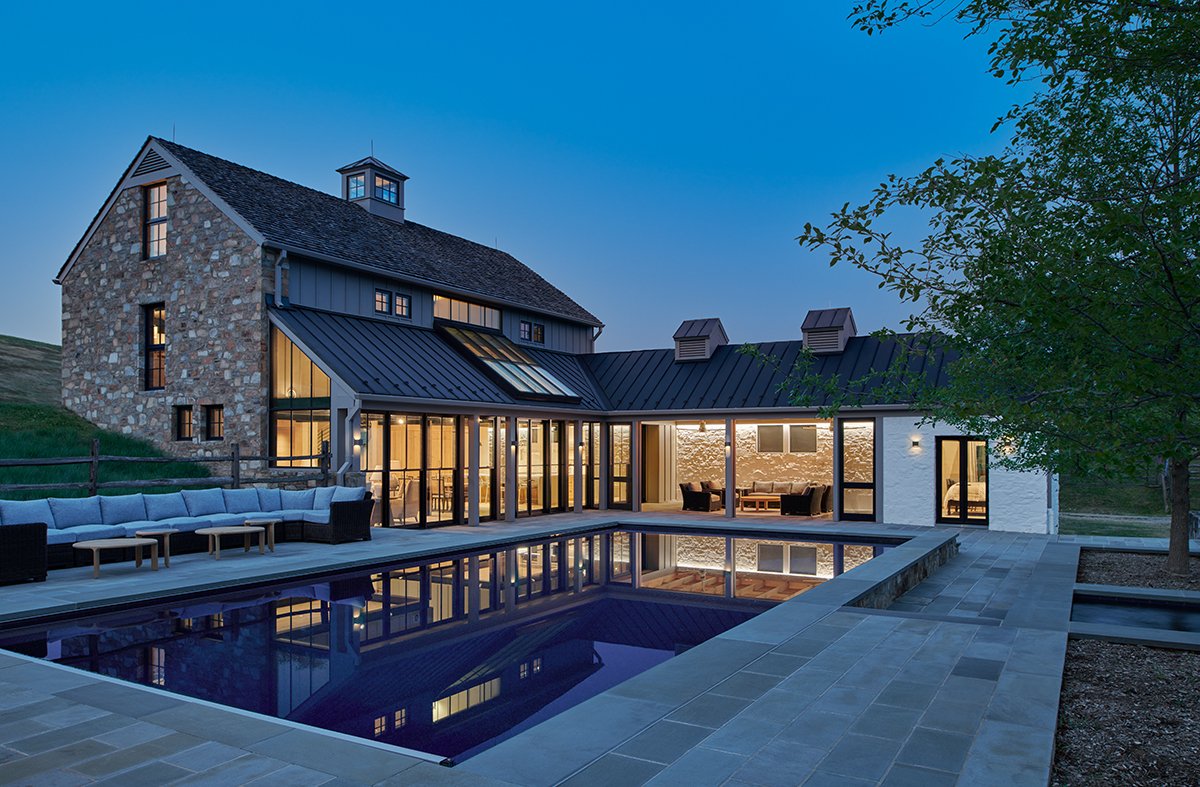
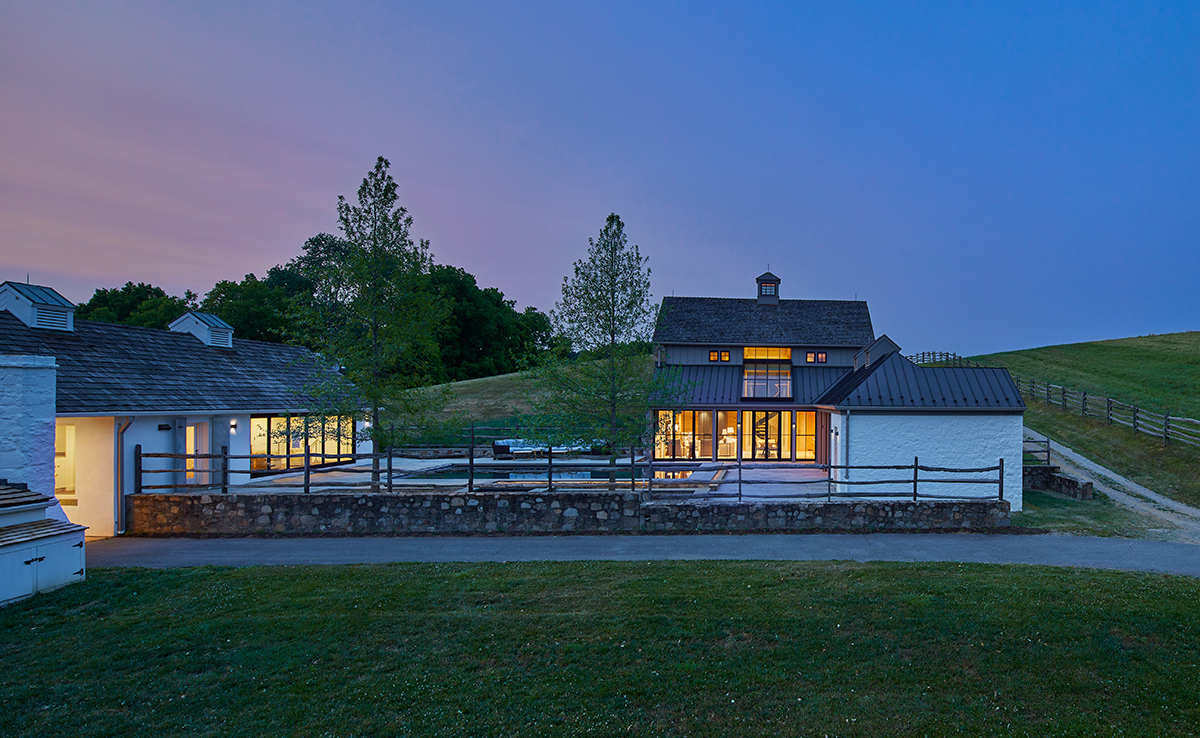
Before Images
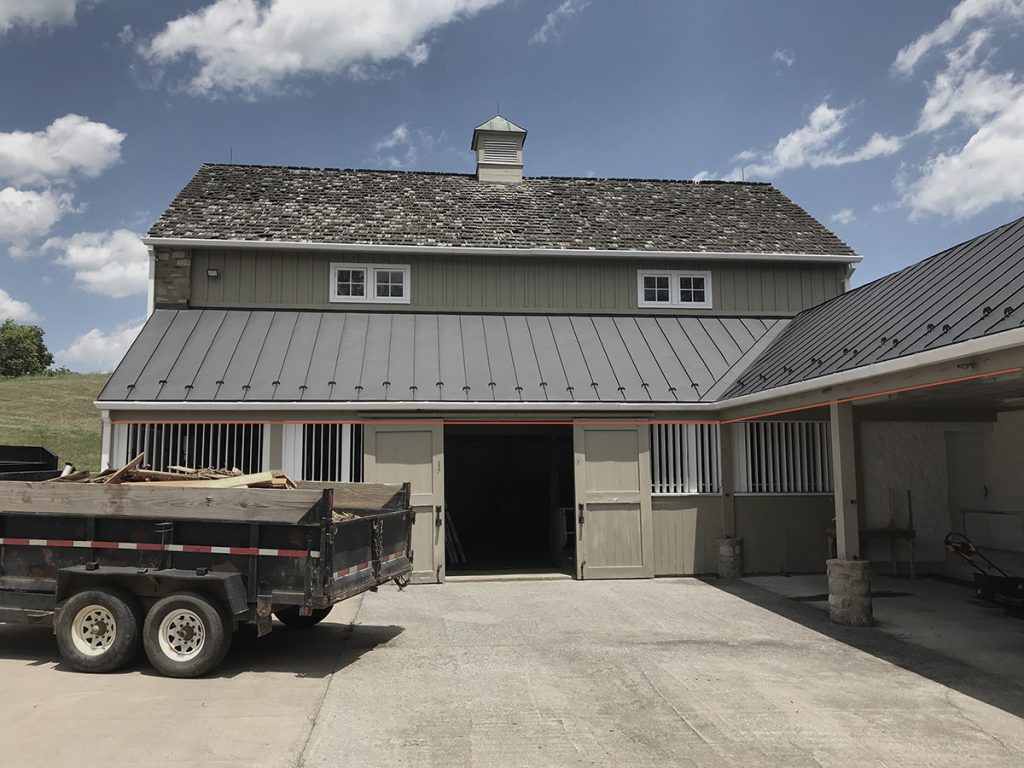
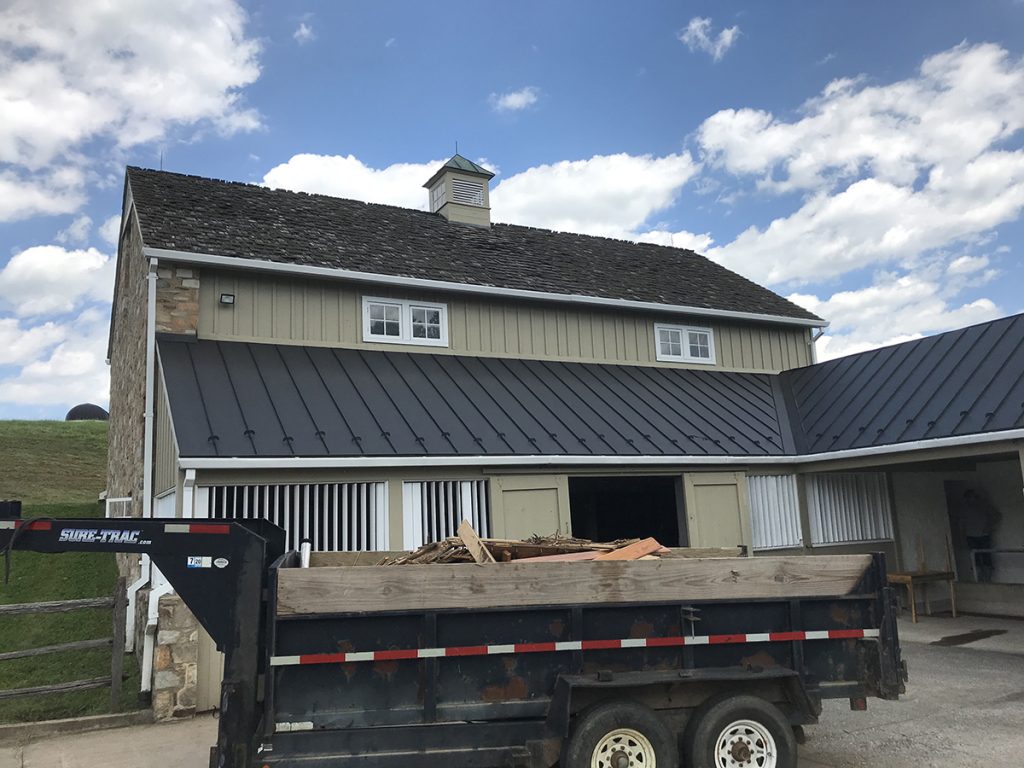
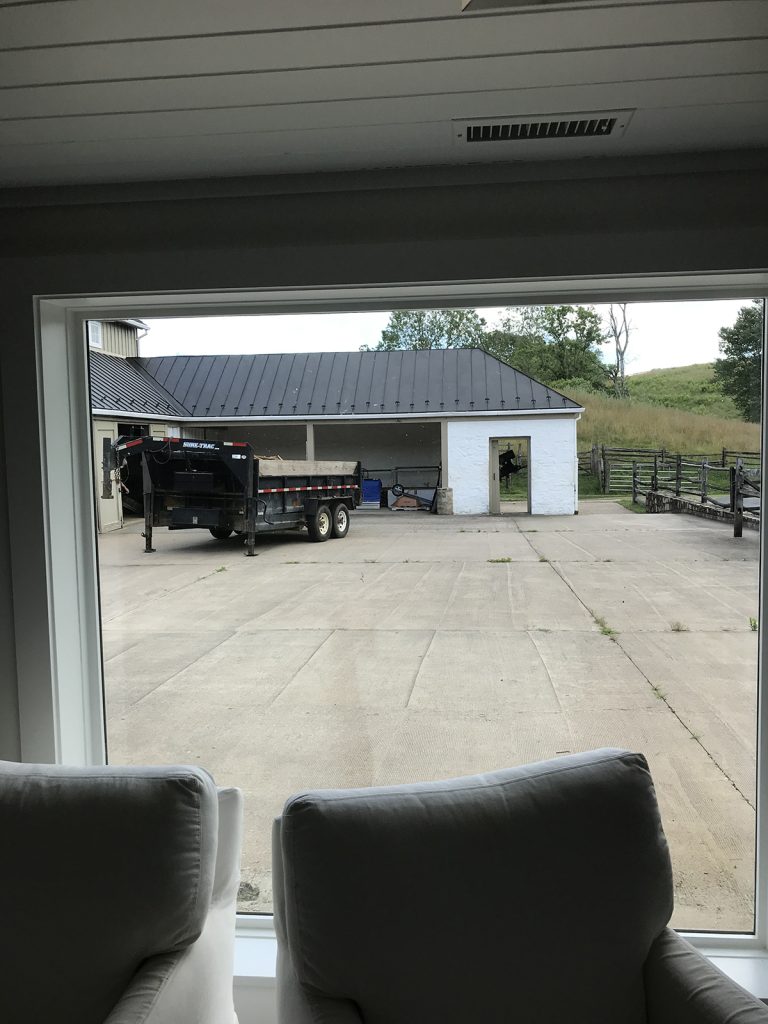
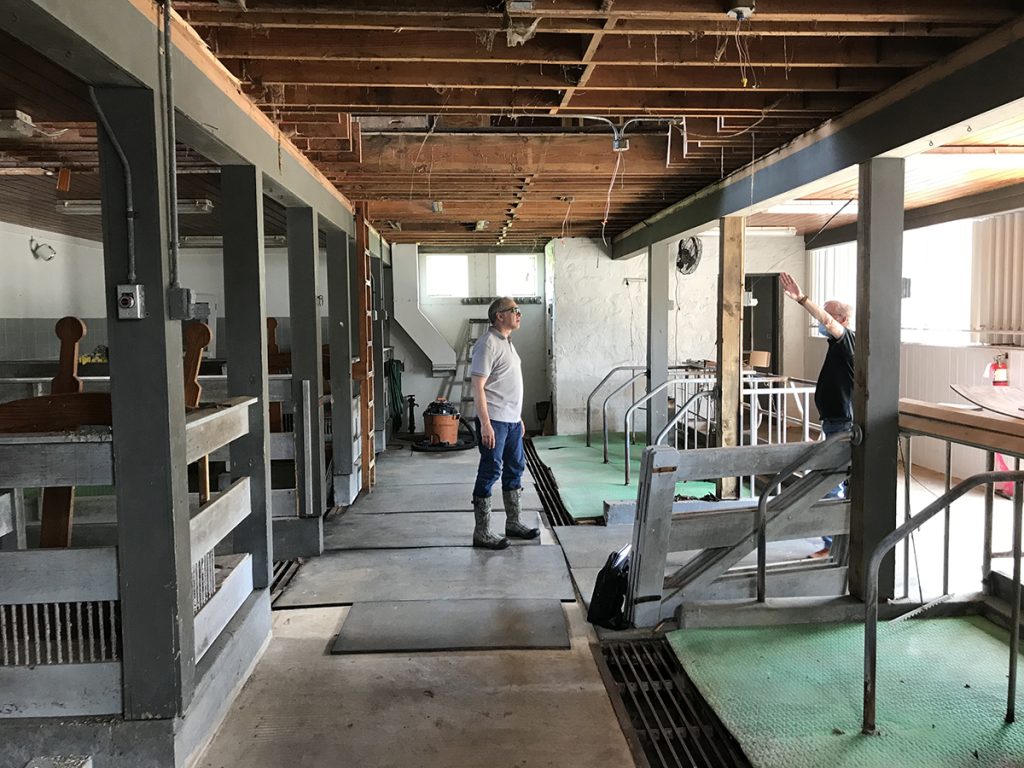
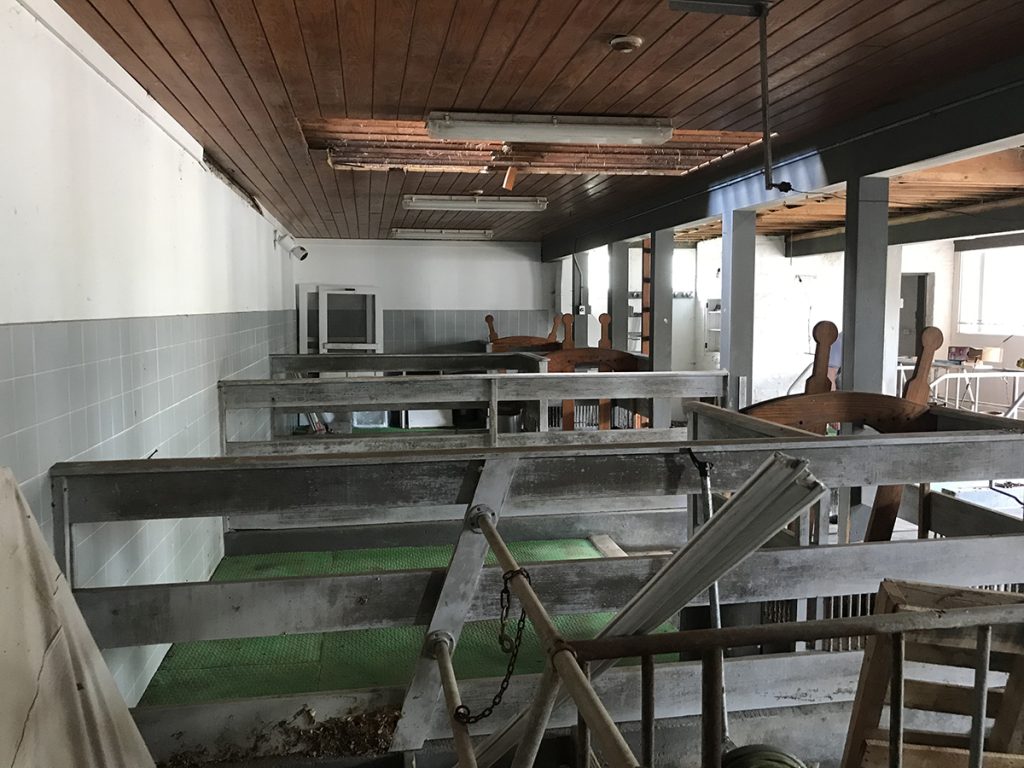
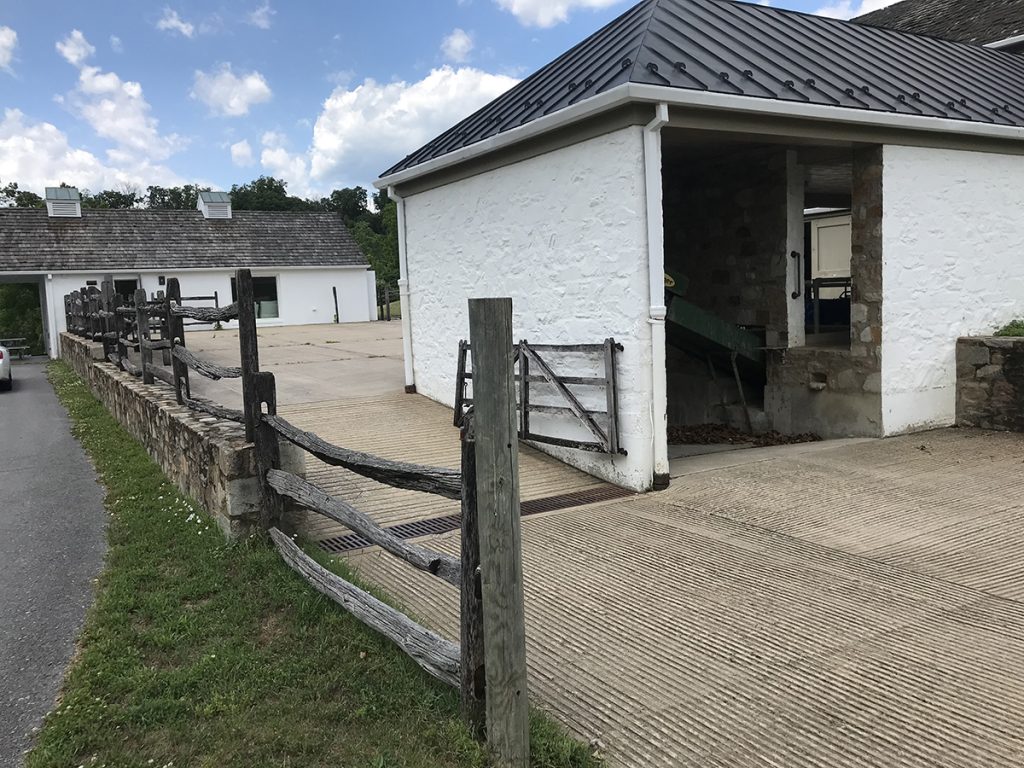
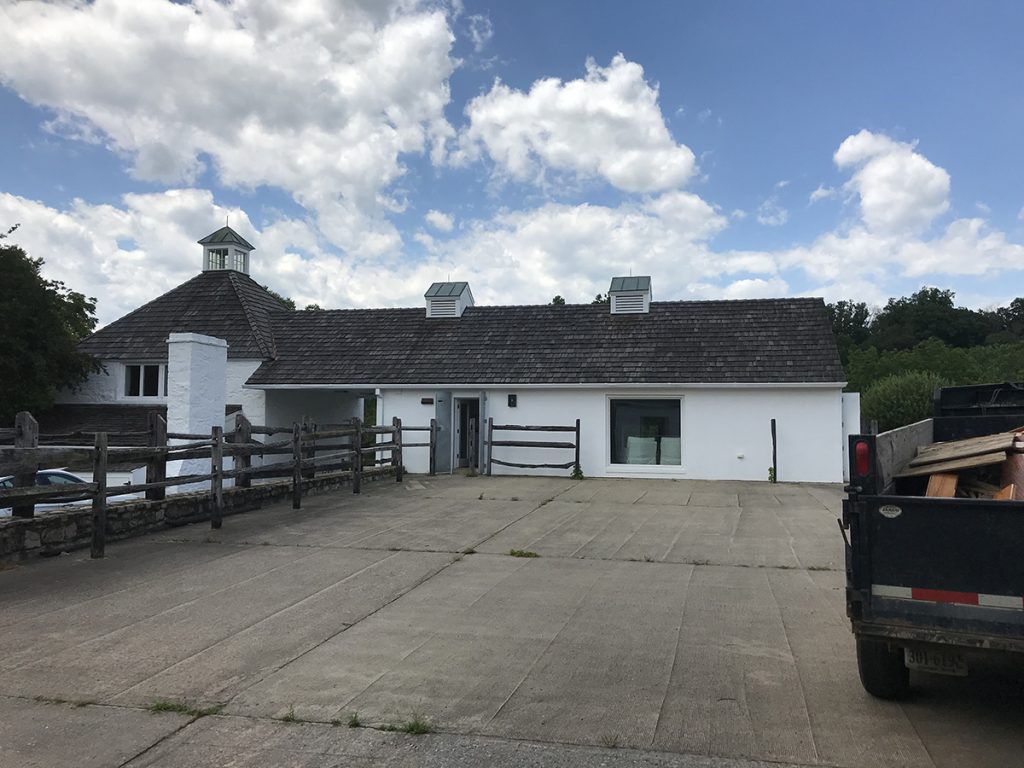

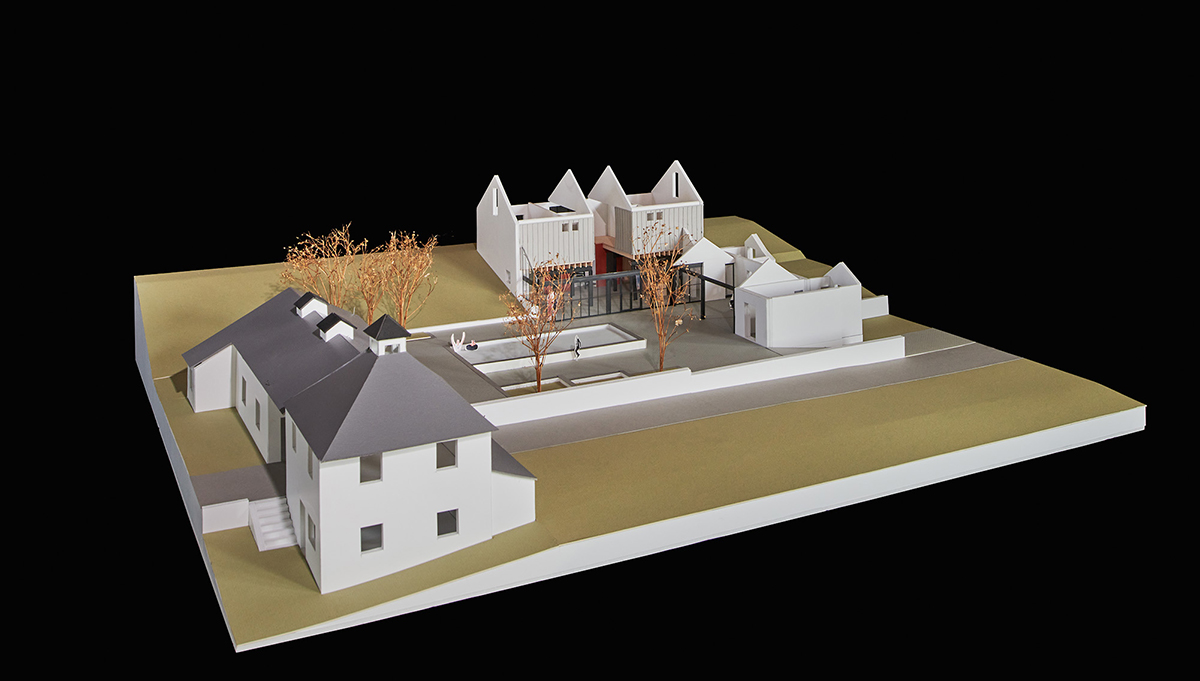
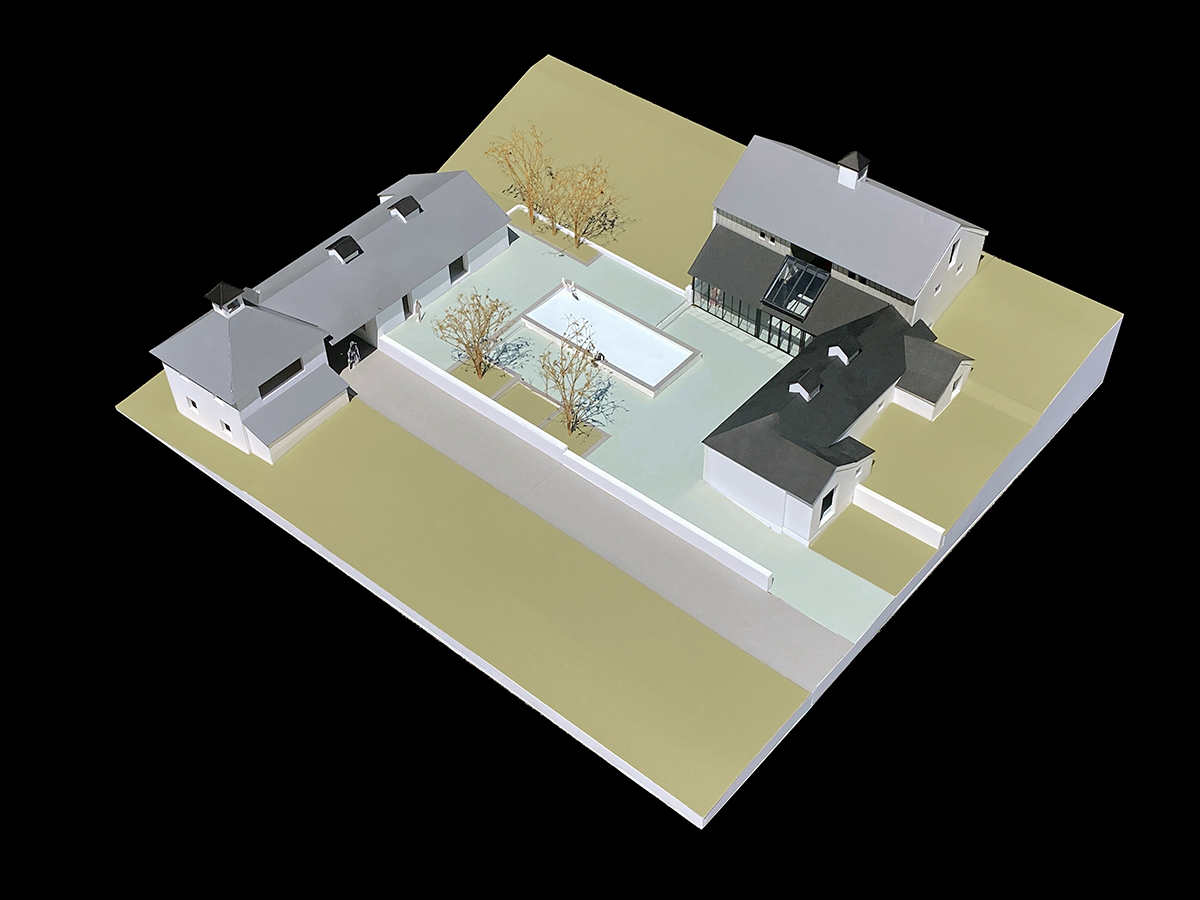
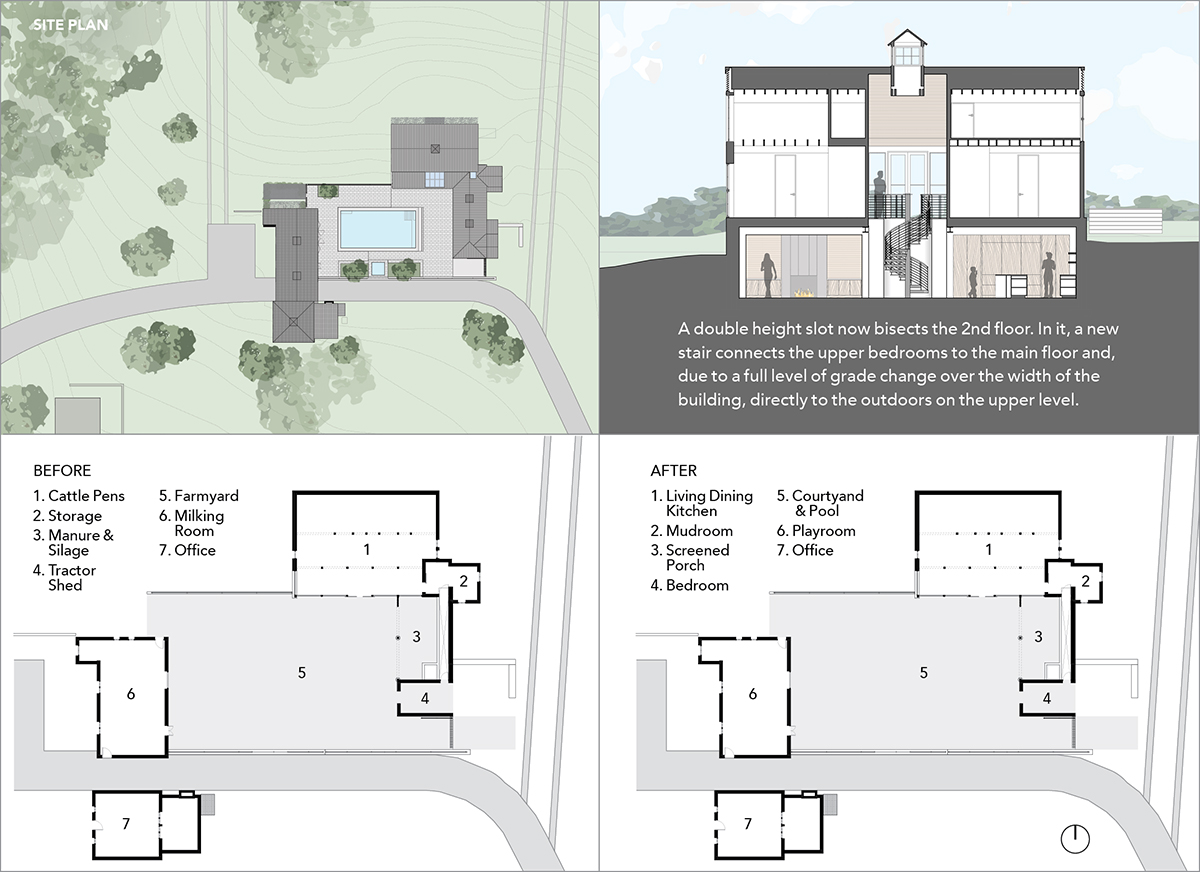
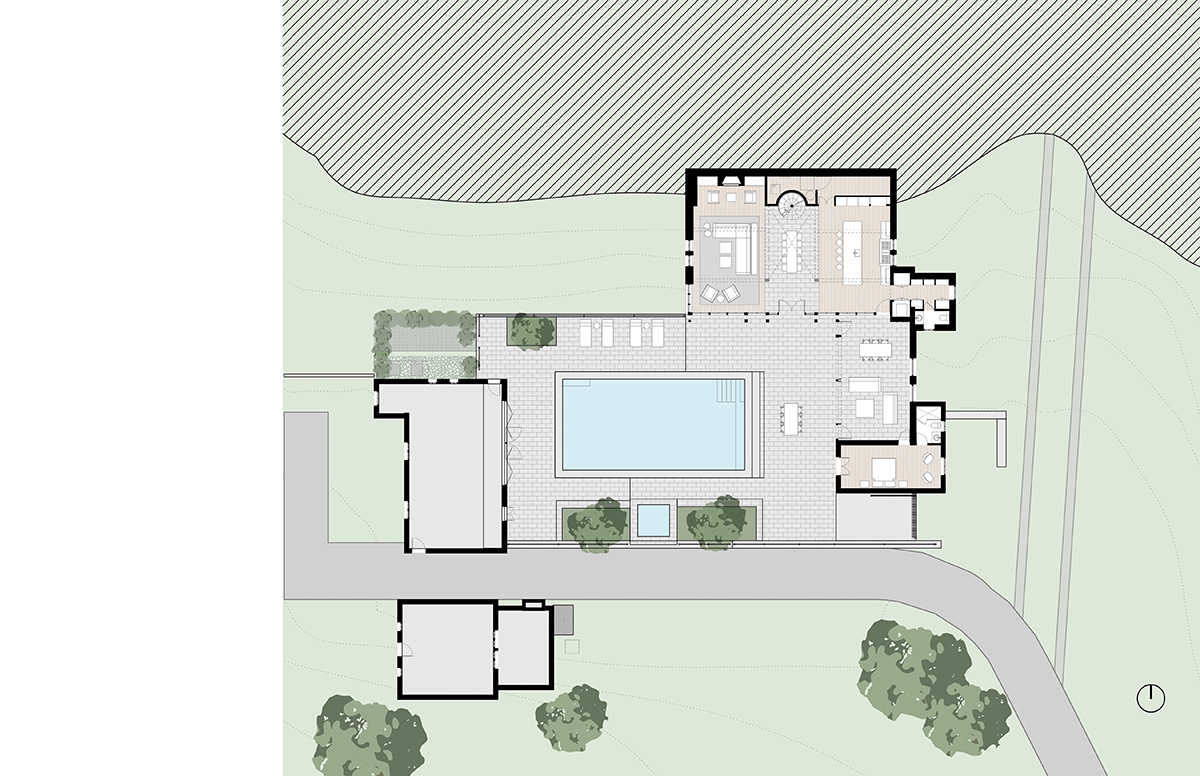
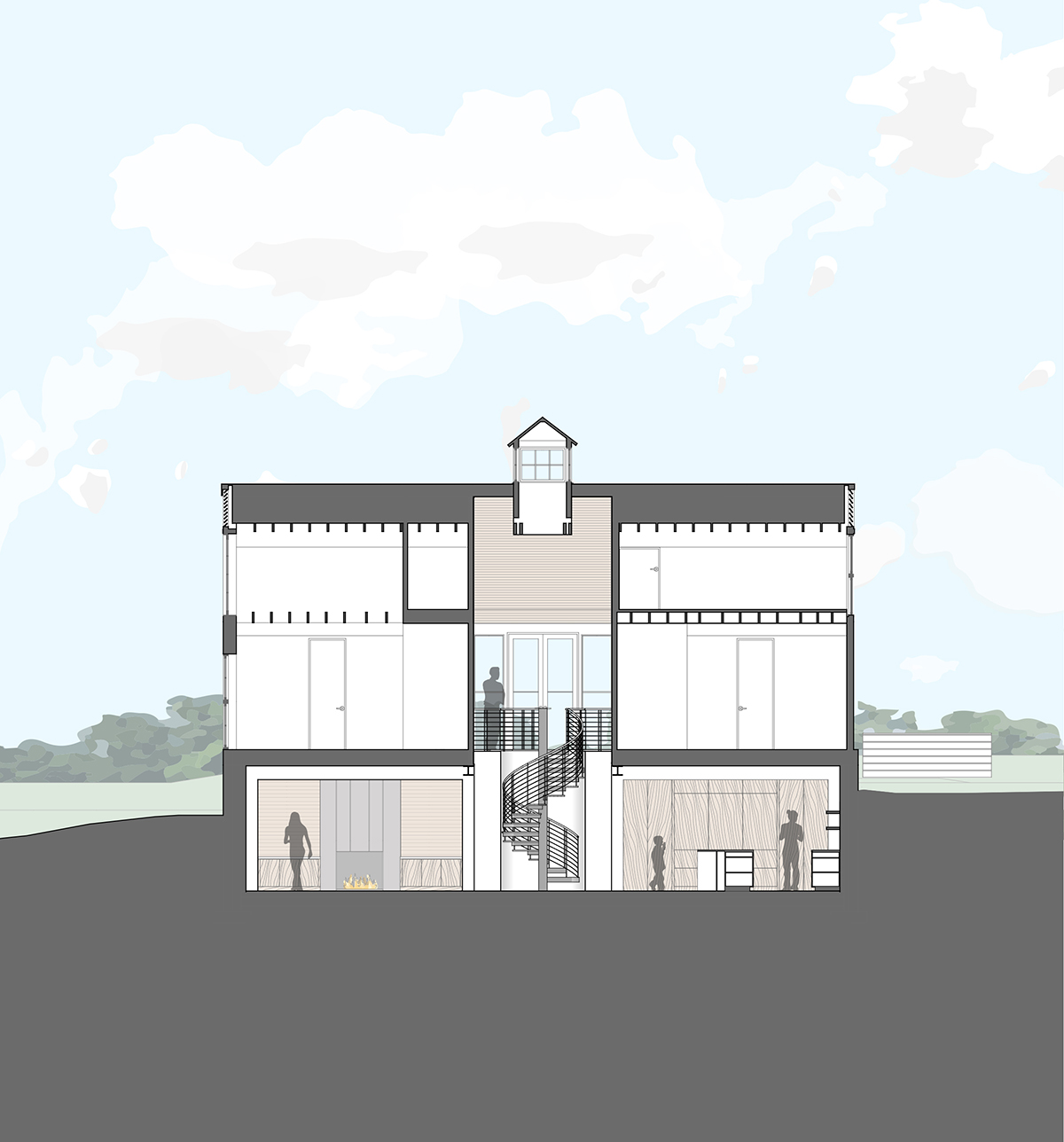
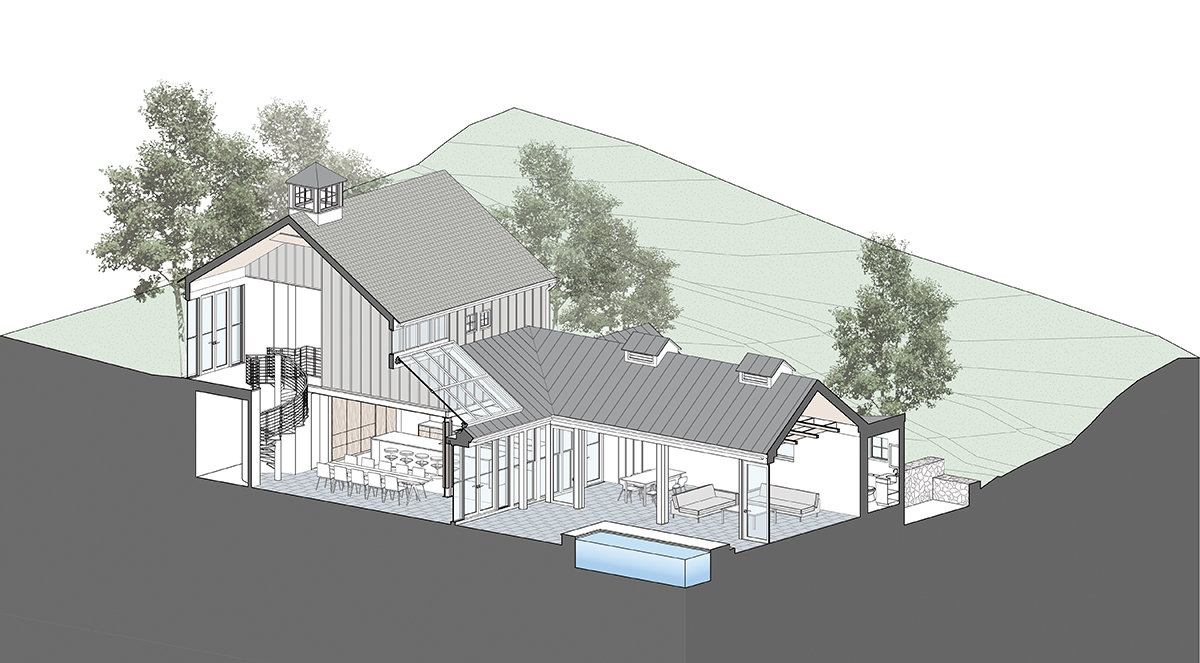
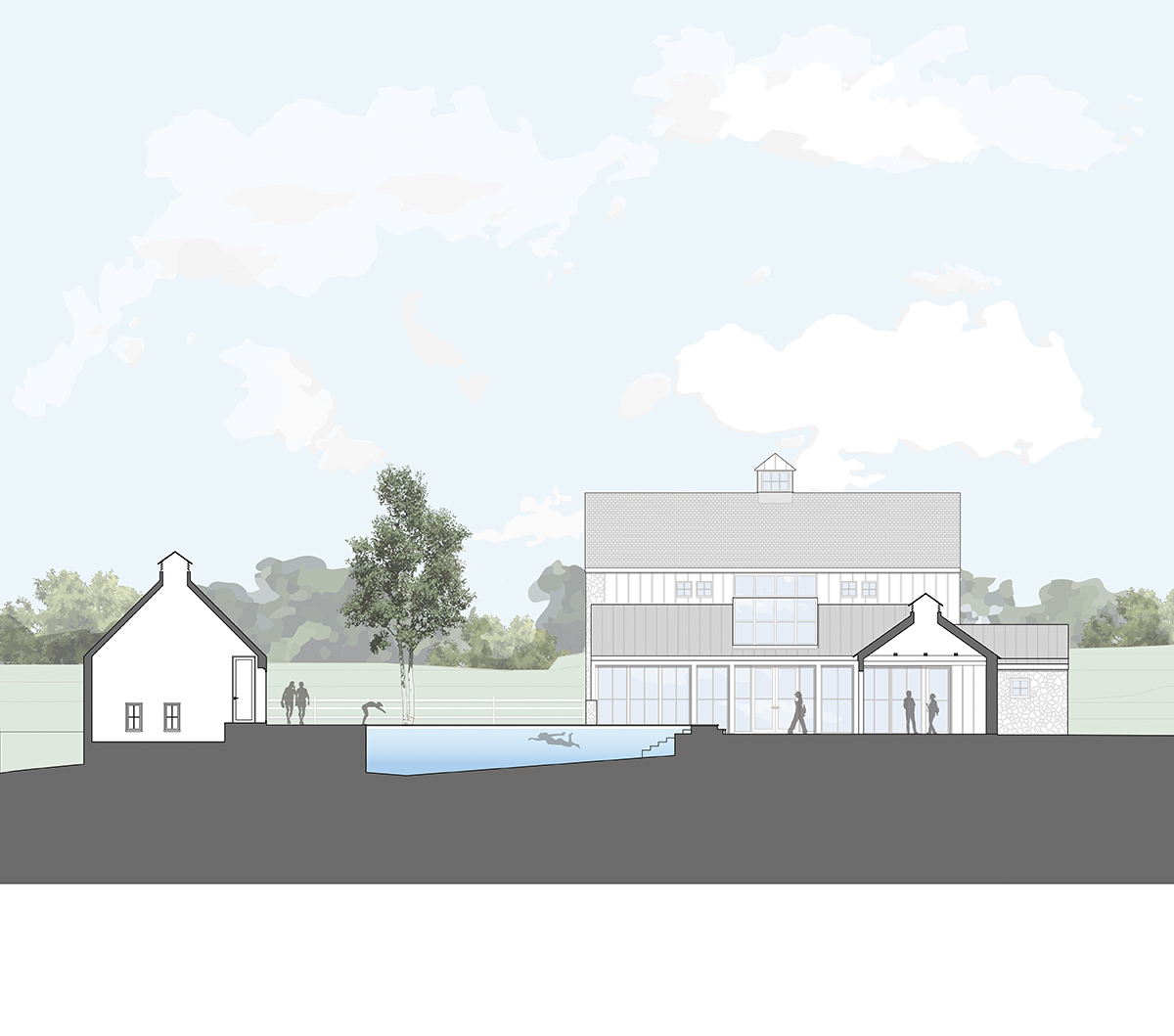
Farm to Table
Rural Virginia
Project Credits
Architect: Mark McInturff, FAIA; Peter Noonan, AIA, McInturff Architects, Bethesda, Maryland
Builder: Added Dimensions, Takoma Park, Maryland
Interior designer: Pam Bakos, Bakos Interiors, Knoxville, Tennessee
Lighting designer: Wayne Hinson, Hinson Lighting Design Group, Washington, D.C.
Pool contractor: Lewis Aquatech, Chantilly, Virginia
Civil engineer: Greenway Engineering, Winchester, Virginia
Project size: 2,500 square feet
Site size: Withheld
Construction cost: Withheld
Photography: Anice Hoachlander; Peter Noonan (before photos)
Key Products
Cabinetry/Passage Doors/Vanities: Coastal Cabinets
Cooking ventilation: Zephyr
Cooktop/range: Wolf
Countertops: Marble Systems Albatre Blanc
Diffusers: Shoemaker Manufacturing
Dishwasher: Bosch
Drywall: USG
Engineered lumber: Trus Joist International
Entry doors: Loewen Windows
Exterior cladding: James Hardie
Exterior lighting: BK Lighting, Klus
Interior lighting: Tech Lighting, Buschfeld, Soraa, MP Lighting, Eklipse Lighting, Revelite, LTF
Fans: Big Ass Fan
Fasteners: Simpson Strong-Tie
Faucets: Rohl, Marzi, O’NEIL RUPPEL, Kohler
Fireplace: Superior Fireplaces
Hot tub/spa/sauna: Custom, Lewis Aquatech
Housewrap: Tyvek
Icemaker: Scotsman
HVAC systems: Carrier
Ovens: Wolf
Paints/coatings: Benjamin Moore, Tadelakt
Radiant heating: Warmboard
Refrigerator: Sub-Zero
Roofing: Cedar shakes
Sheathing: Huber ZIP System
Sinks: Kohler, Marzi, Stone Forest (powder room)
Skylights: Wasco
Stairs: Duvinage
Toilets: TOTO
Ventilation: Fantech
Window shading systems: Lutron
Windows and window wall systems: Loewen
Wine refrigerator: Sub-Zero
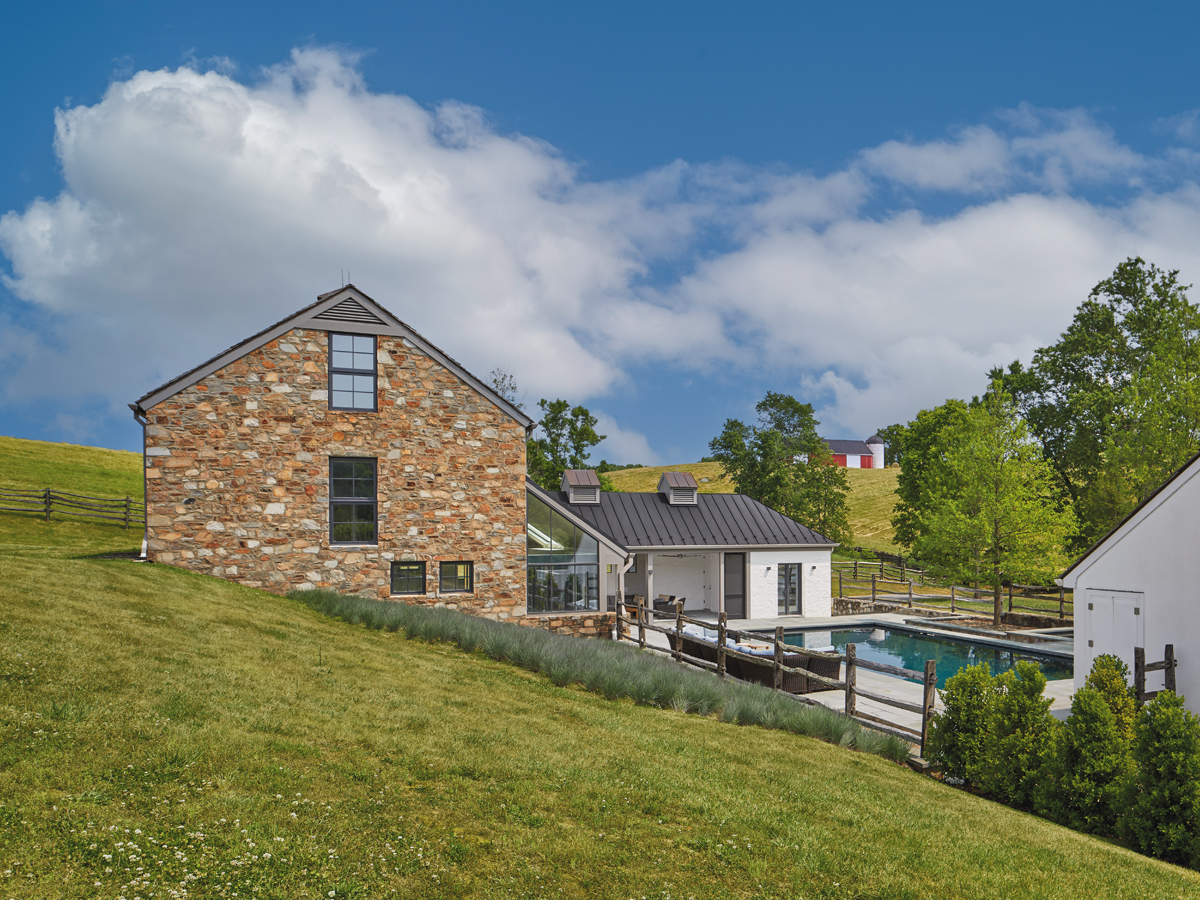
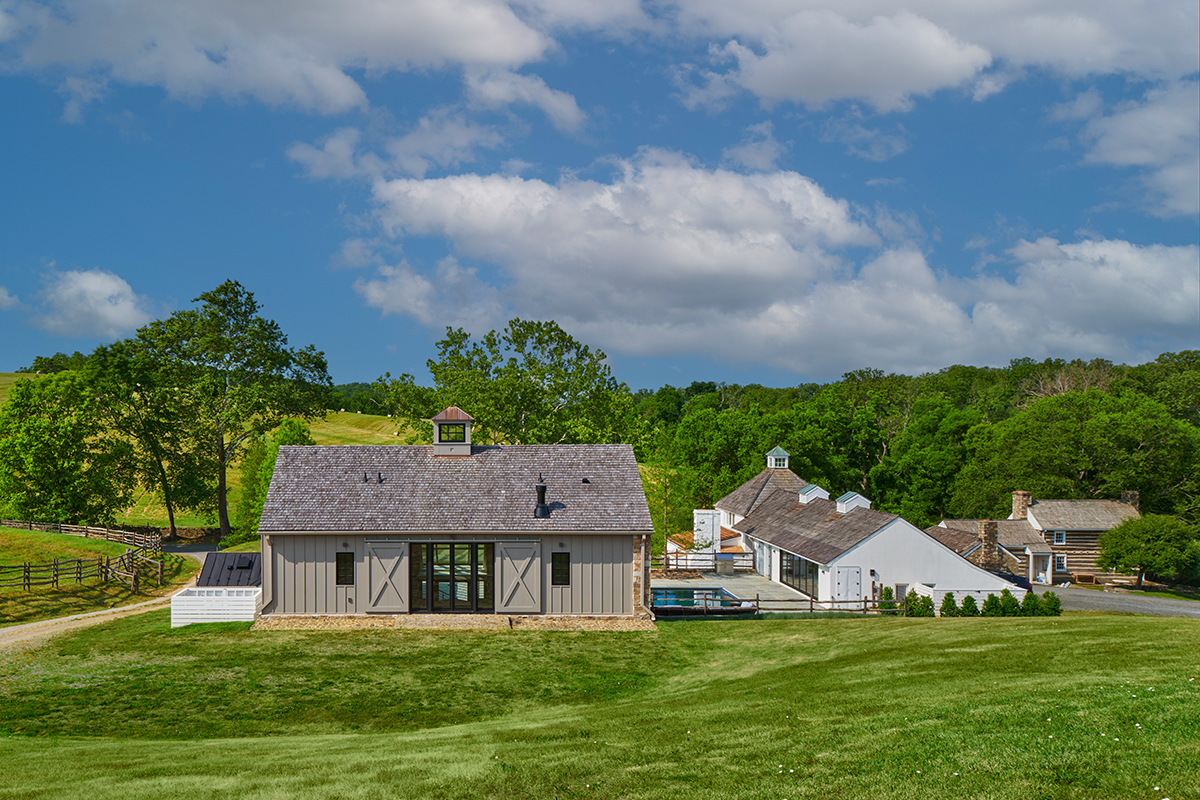
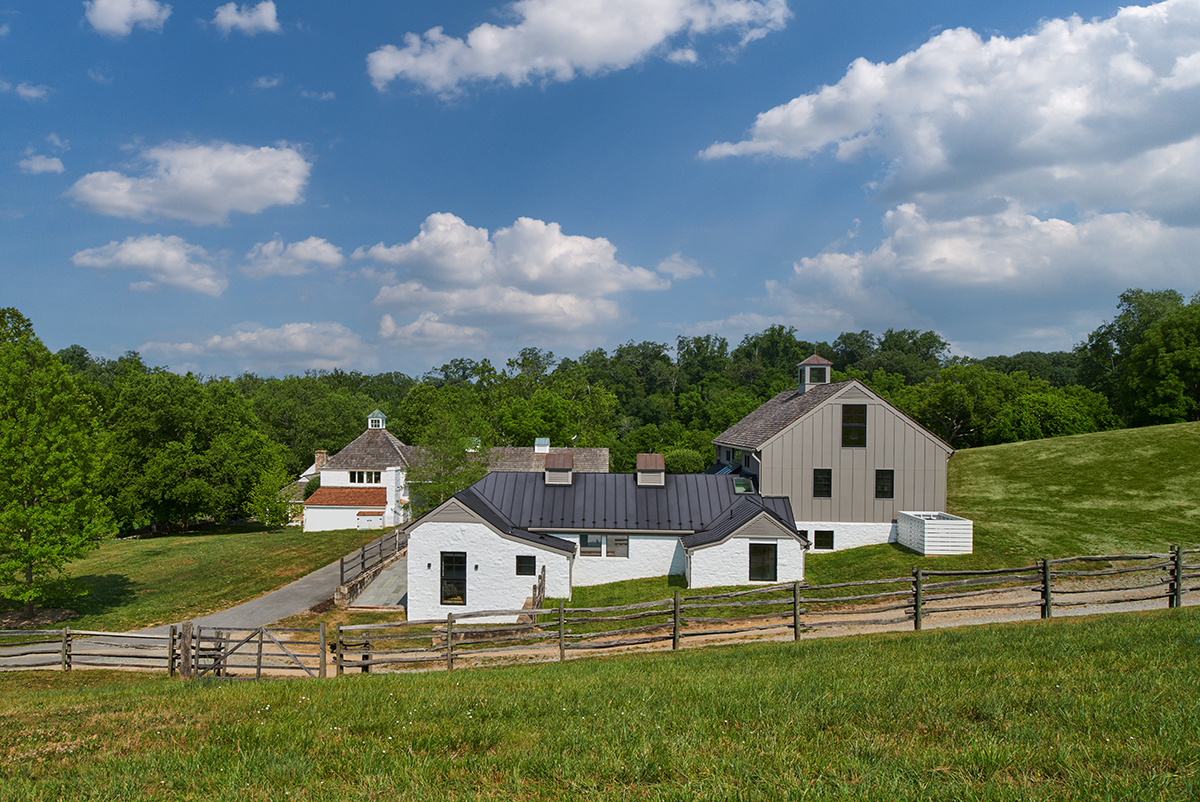
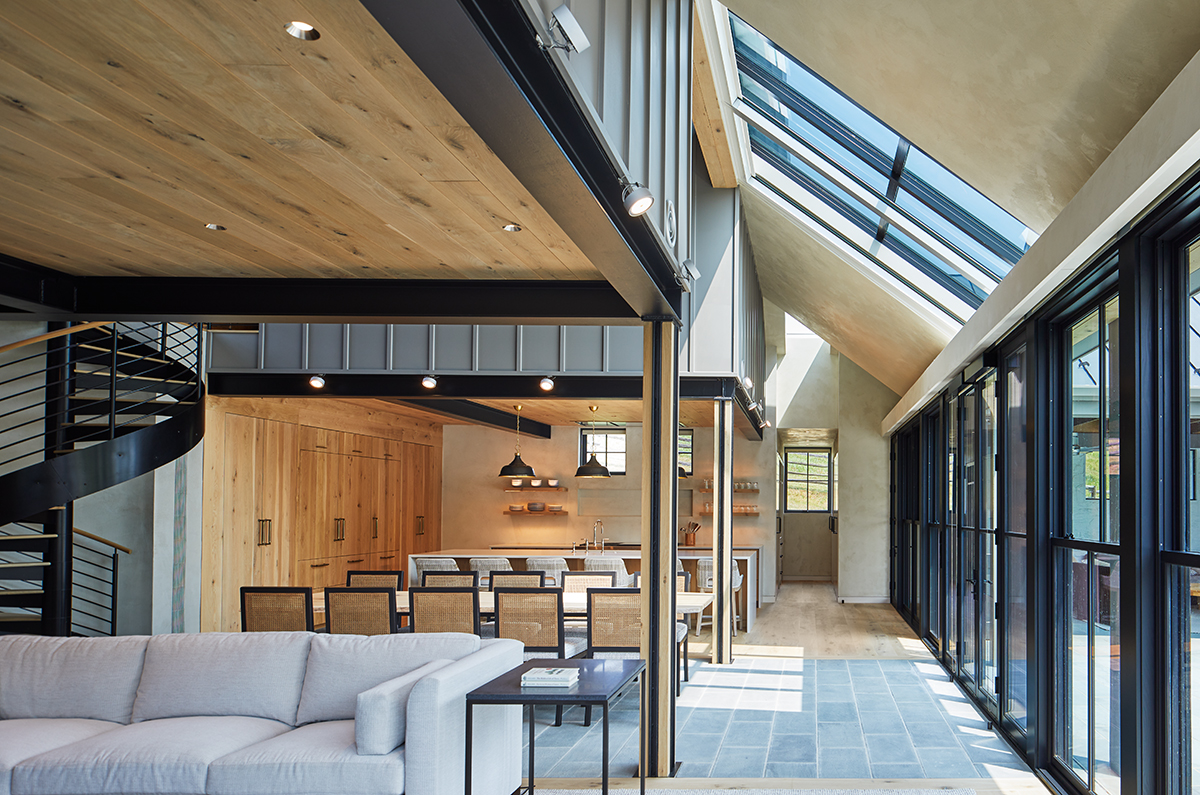
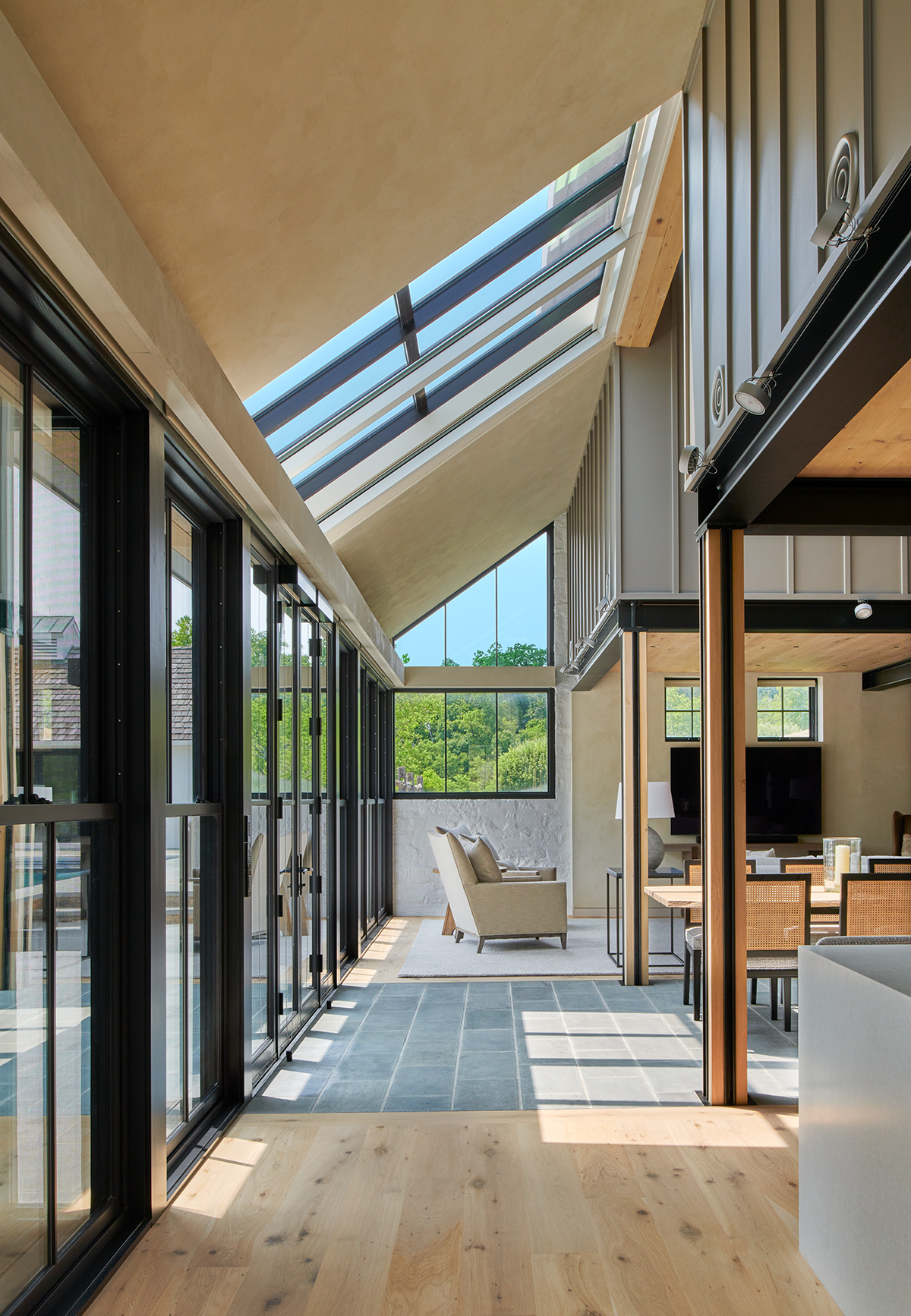
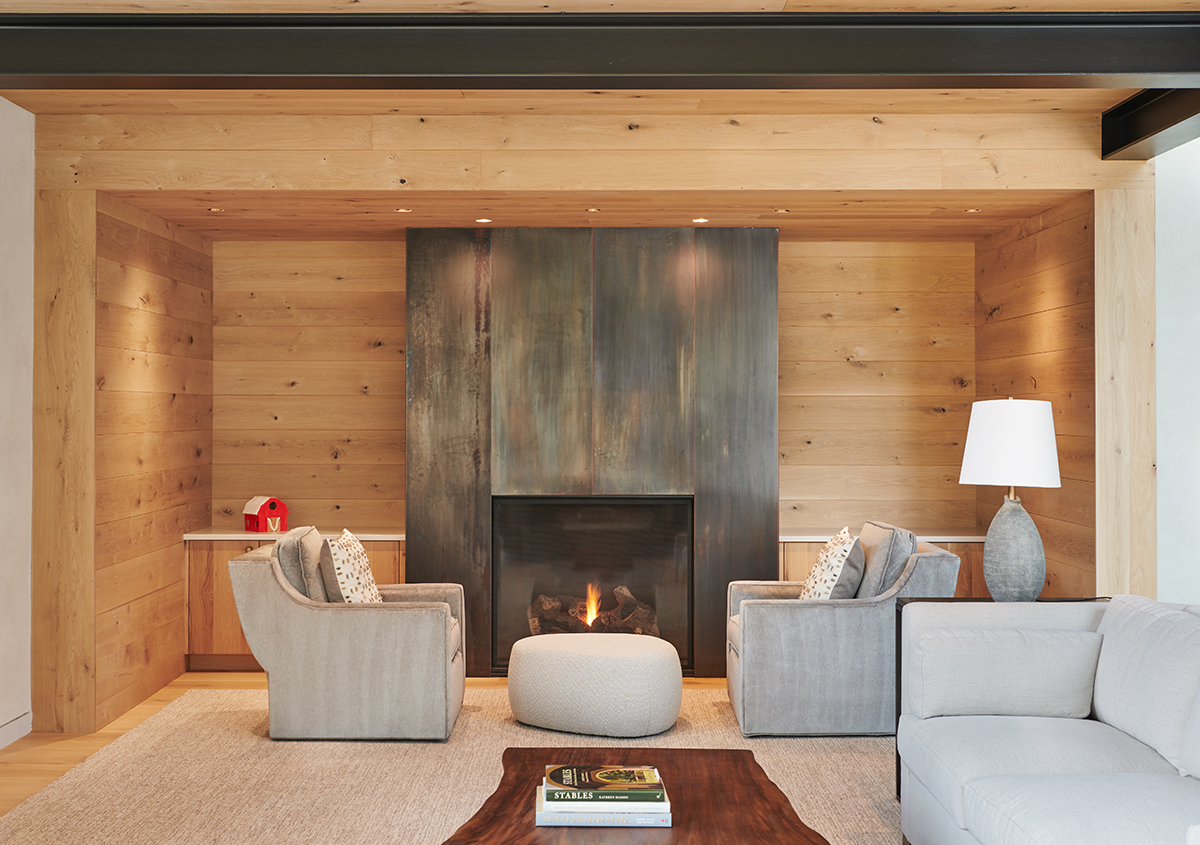
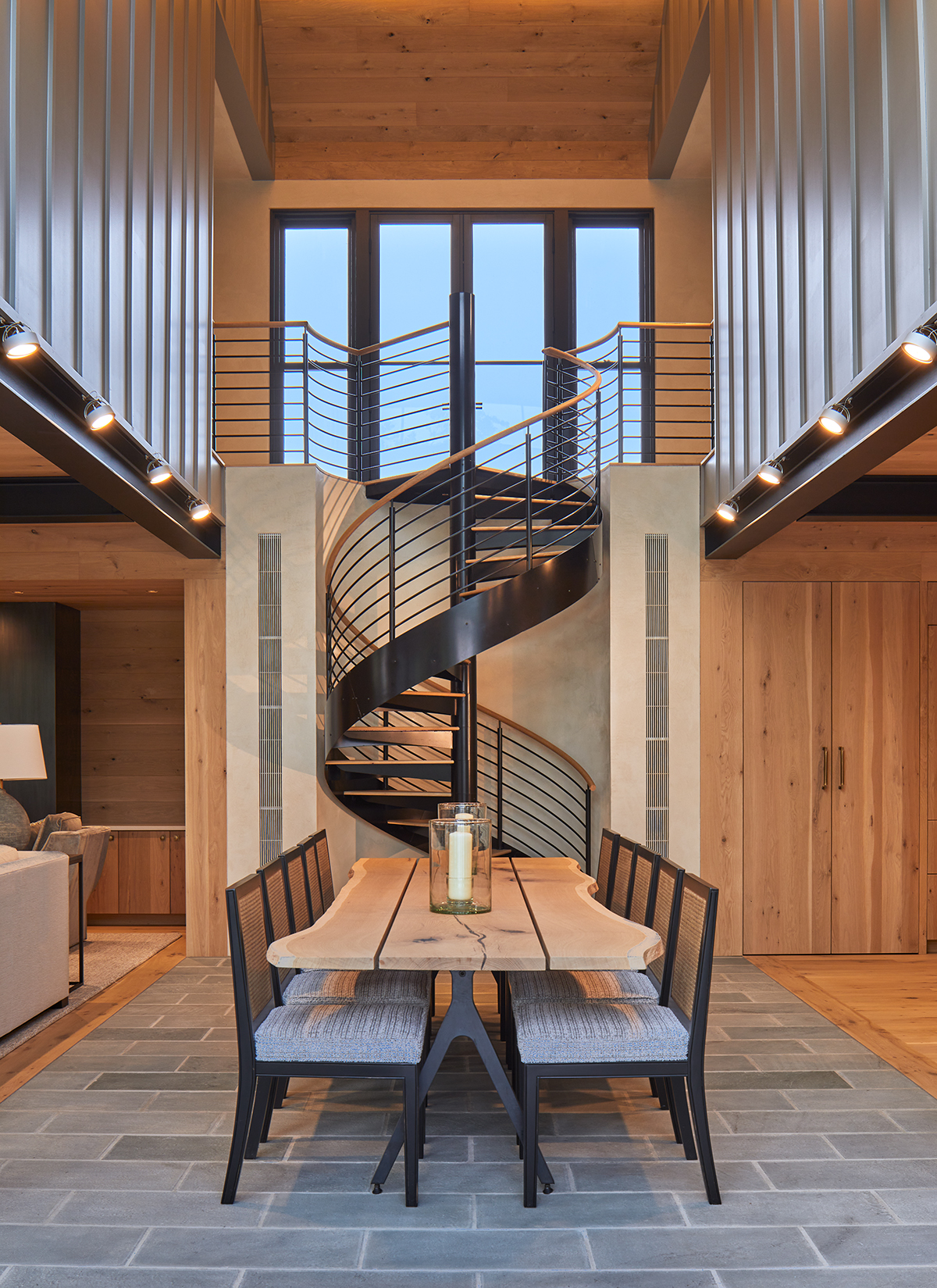
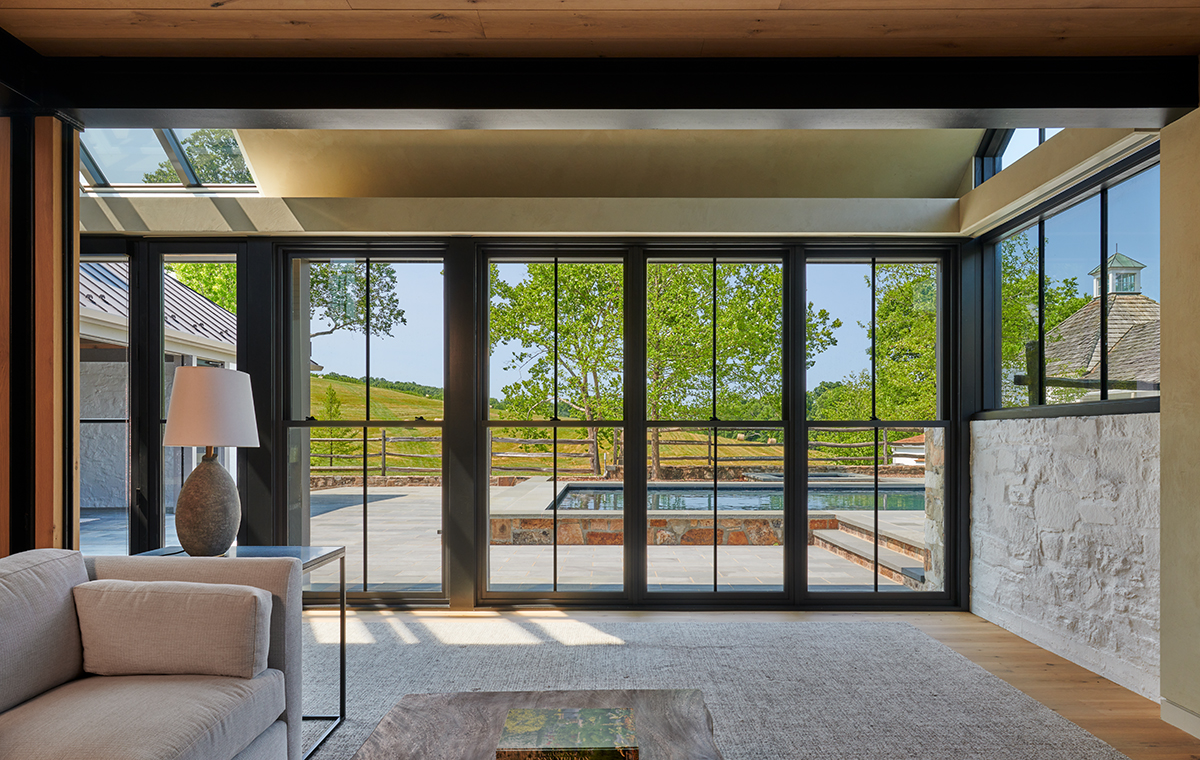
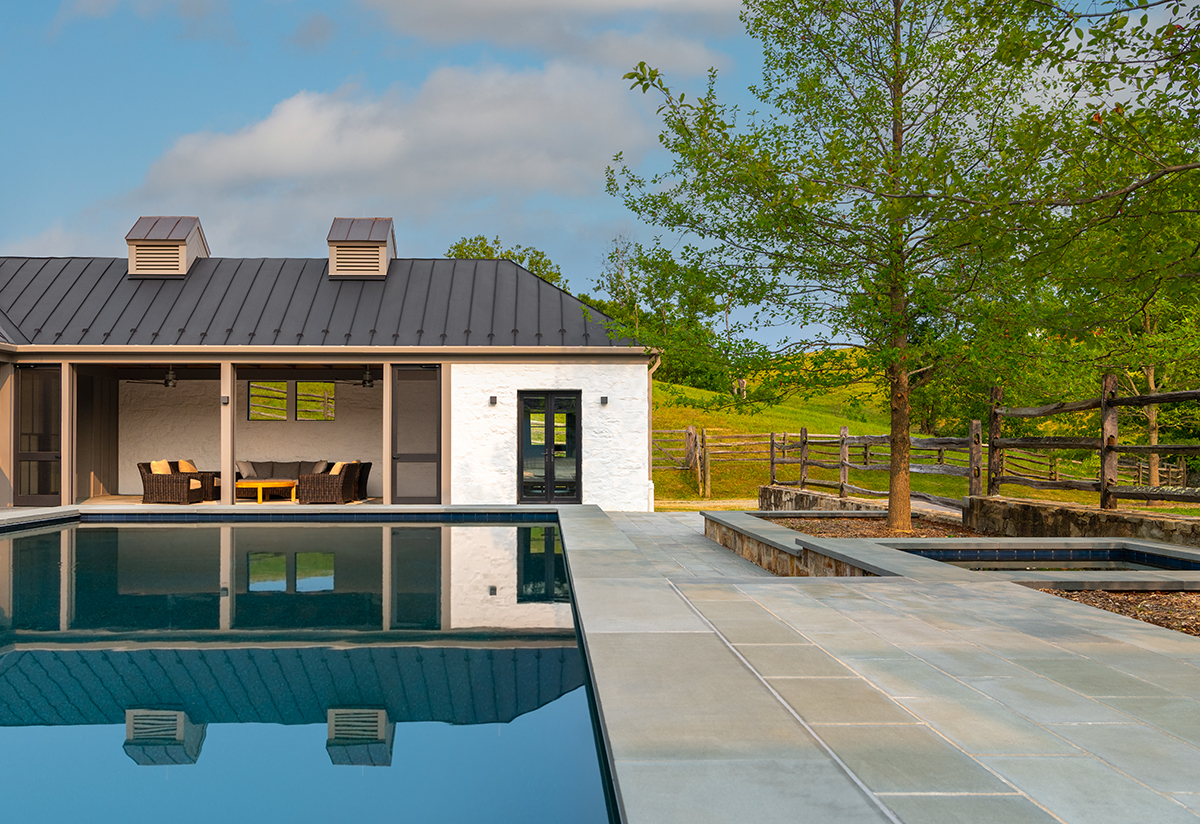
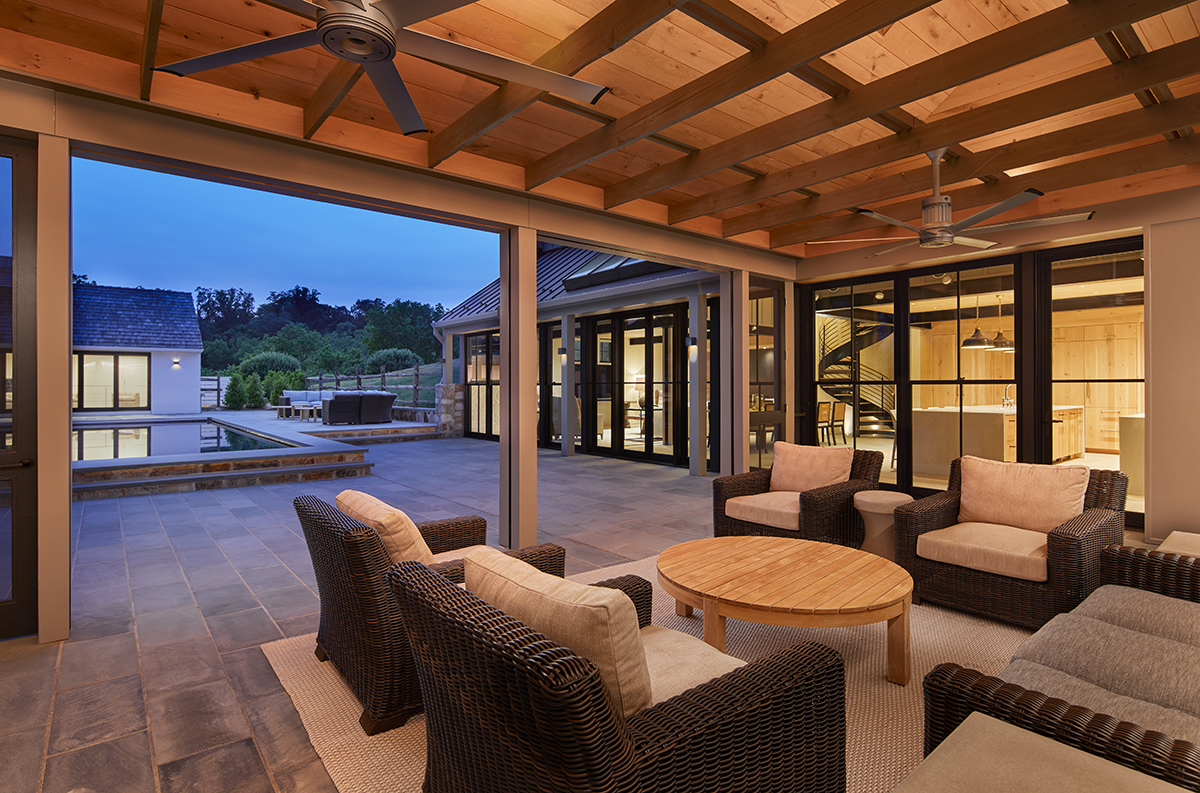
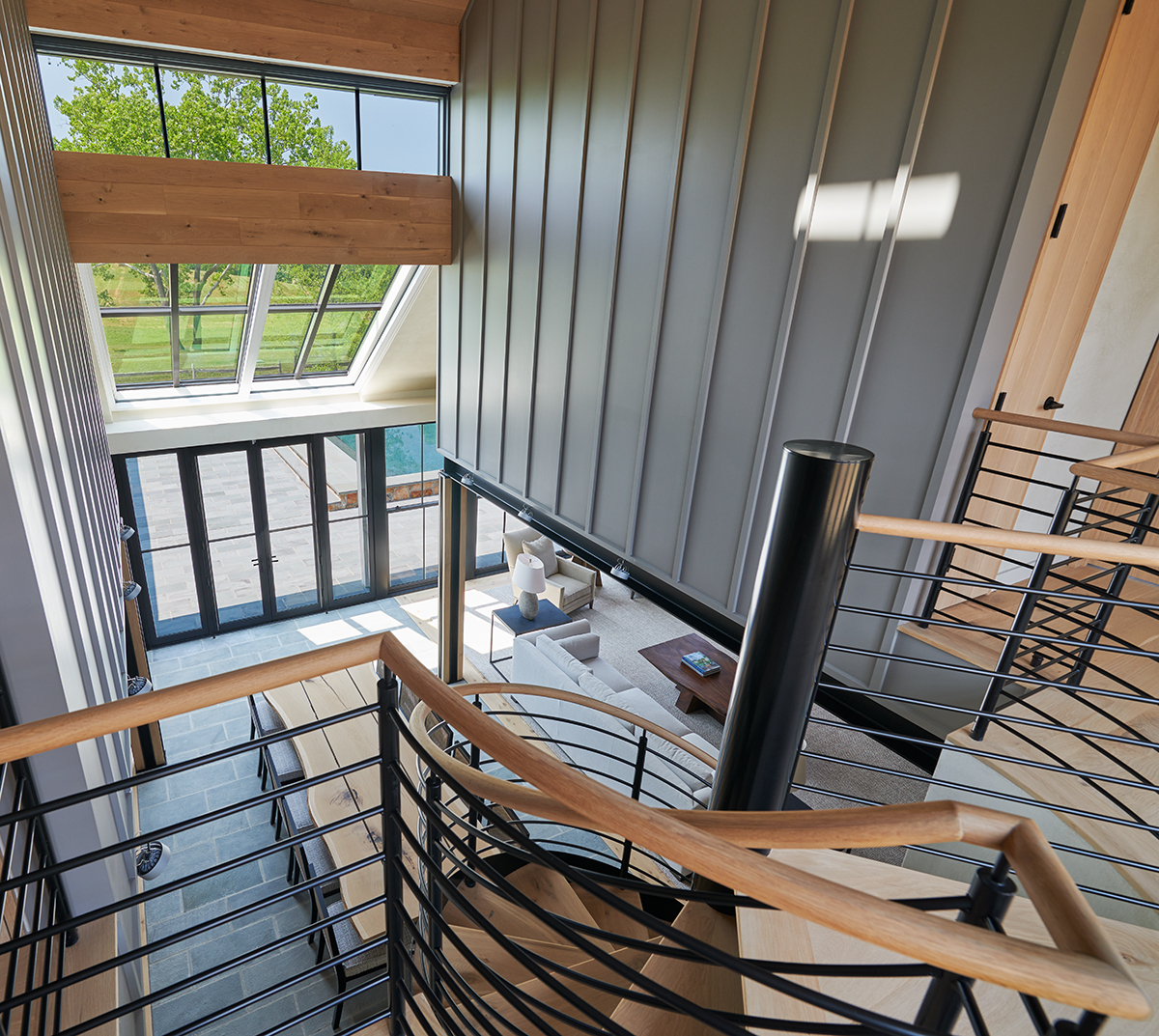
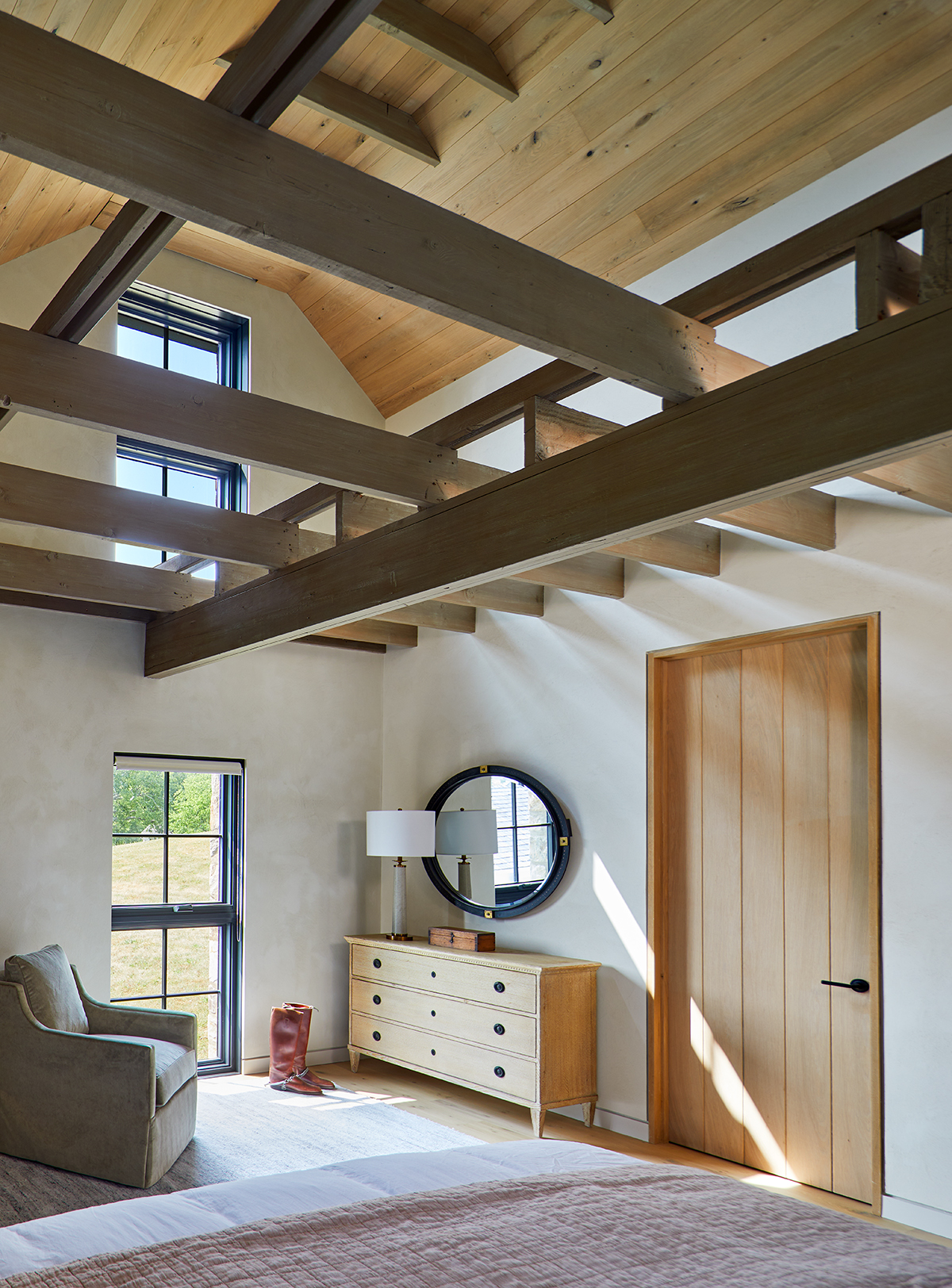
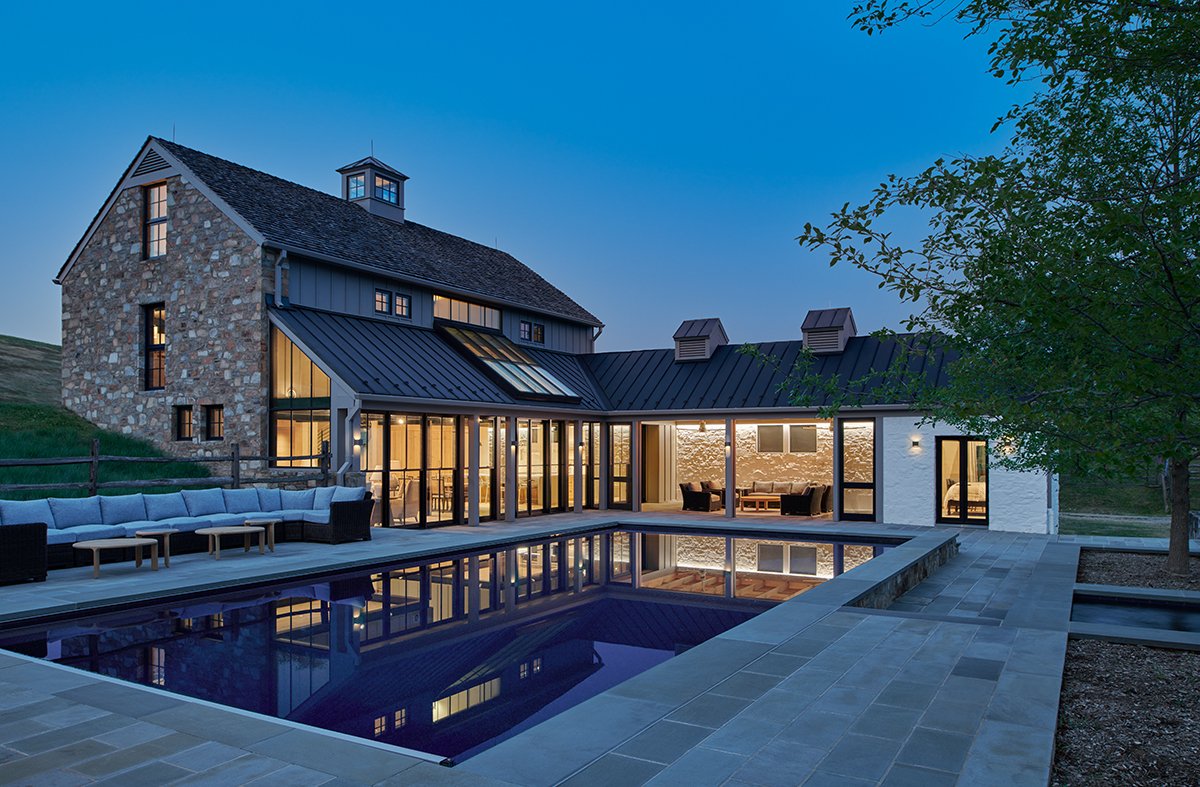
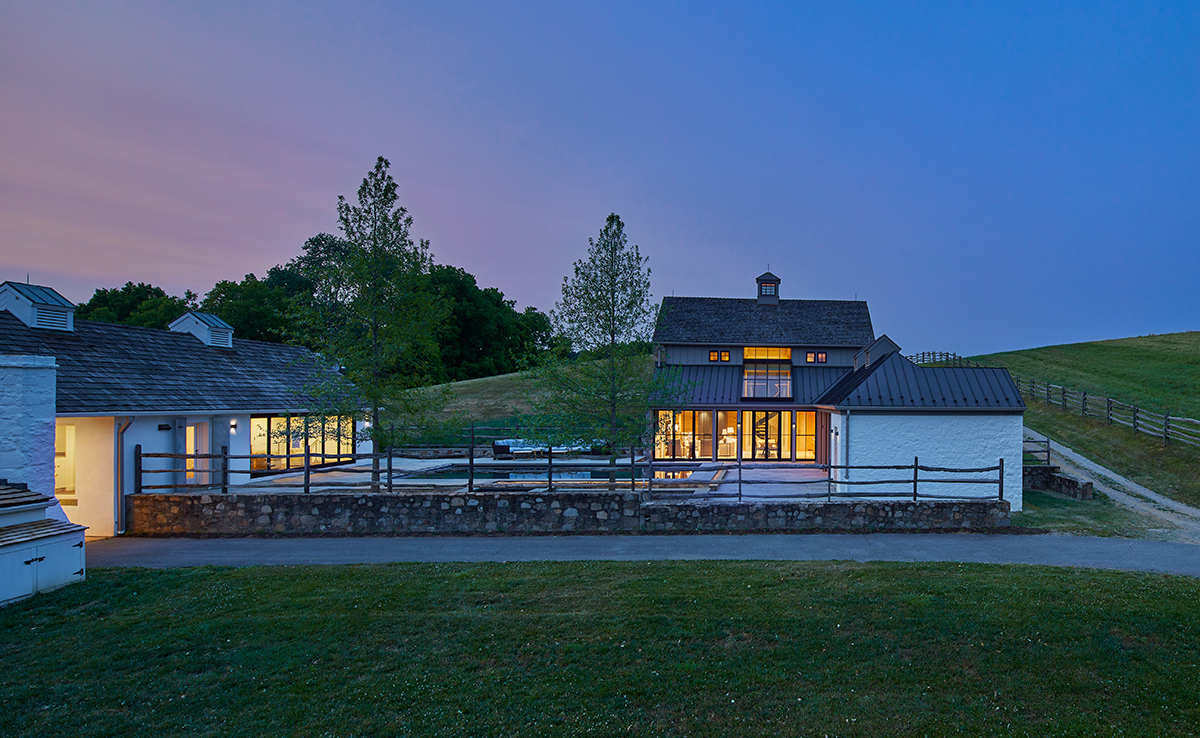